Wastewater Nutrient Removal Helps Preserve the Chesapeake Bay
(Updated October 2021)
Wastewater managers are not known to be risk takers. The prevailing attitude is better to be safe than sorry. On the other hand, it is necessary to take risks in order to achieve maximum results. Nothing ventured, nothing gained. Marty Johnson (pictured), Chief Plant Operator of the Seneca Wastewater Treatment Plant in suburban Washington, D.C., understands that very well as it pertains to nutrient removal from wastewater. “I like to experiment and tinker. In order to do that I need equipment that works well.” The YSI IQ SensorNet process monitoring system has earned the trust of the Seneca operations team by providing reliable continuous monitoring of parameters critical for optimizing the nutrient removal system at the water resource recovery facility (WRRF*). “There is no drift with the YSI nitrate sensor. I can rely on the measurement,” says Marty.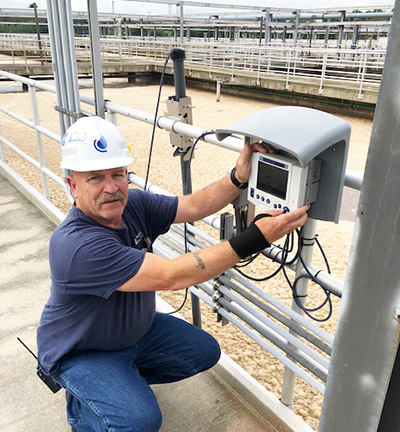
The nutrients that typically need to be addressed by WRRFs are nitrogen and phosphorus, both of which exist naturally and are critical components of healthy ecosystems. Naturally-occurring types of nitrogen include ammonia, nitrite, and nitrate, and levels are typically low – less than 1 mg/L. On the other hand, the discharge of a WRRF can contain levels as high as 30 mg N/L, primarily in the form of nitrate (NO3-), which can wreak havoc on any aquatic ecosystem. Certain levels of nitrate are necessary for healthy plant growth, but excessive amounts of nitrate in estuaries and bodies of water can fuel the growth of algal blooms and cause dramatic increases in aquatic plant growth, impacting dissolved oxygen (DO) levels (creating hypoxic dead zones that suffocate marine life), temperature, and other parameters. The Chesapeake Bay is a case in point. It experienced a decline in water quality due to over-enrichment of nutrients (mainly phosphorus and nitrogen).
The Washington Suburban Sanitary Commission (WSSC) serves 1.8 million residents of central Maryland. Its proximity to the Chesapeake Bay creates a unique environmental concern. WSSC was assessed new discharge requirements for allowable nitrate in treated effluent in order to achieve nitrogen loading reduction commitments set forth in the Chesapeake Bay Program. For the WSSC Seneca facility, a new denitrification process was required as part of an upgrade to achieve enhanced nutrient removal (ENR). The primary goal for the denitrification process was to implement a solution that reduced total nitrogen (TN) in treated effluent to less than 4.0 mg N/L, and to minimize operating costs as much as possible. A 4-stage Bardenpho configuration with supplemental external carbon addition (methanol) was designed and constructed to achieve nitrogen removal requirements.
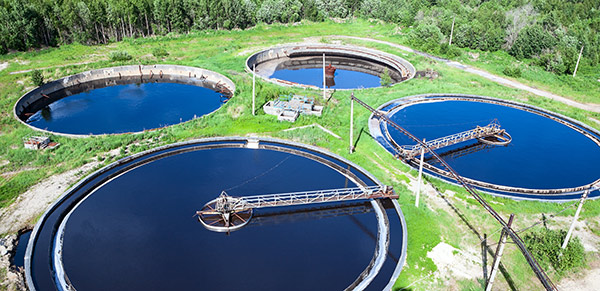
In order for operations to meet the stringent treatment requirements, the Seneca team needed monitoring technology that could provide accurate, real-time data to continuously keep an eye on the process. This would also open the door for implementing additional automation for certain processes of the plant. The Seneca facility had been using online optical UV nitrate monitoring technology for many years but the existing equipment was becoming less reliable. The Seneca team decided to take a chance and invite Joe Gunn, from North East Technical Sales, to come in and provide some options for his team to evaluate.
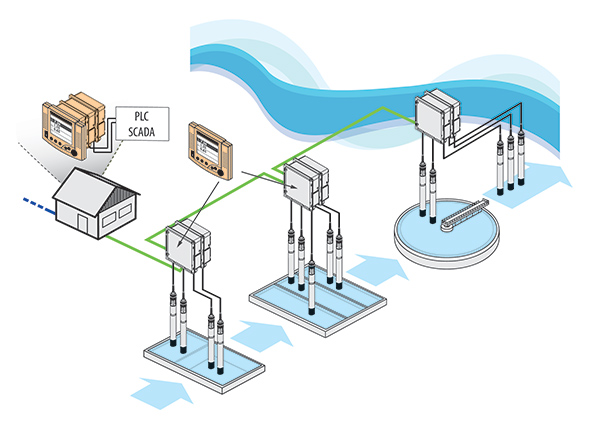
Stackable modules and single-cable design of the IQ SensorNet System
“We had heard about the YSI IQ SensorNet monitoring and control technology, but we needed to see how easy it was to install, and how easy it was to set up and use. Those were all factors that we were looking at. Joe did a side-by-side comparison of two different technologies for us to monitor nitrates,” says Marty. YSI NitraVis® UV Vis nitrate sensors were the preferred technology following the evaluation. (Learn more, Top 5 Questions When Selecting UV or UV Vis Sensors). However, before making a change, the Seneca team was obliged to confirm that the IQ SensorNet was of equal or better quality than their existing equipment by conducting a second demonstration, a head-to-head evaluation with the existing system and a third vendor.
Easy Choice
Not only did the IQ SensorNet system satisfy all the measurement performance requirements, the advantages of IQ SensorNet compared to competitors’ systems were significant. For instance, the UltraClean™ technology of the UV-Vis probe was a major deciding factor. UltraClean is a built-in ultrasonic cleaning technology that prevents biofouling and lowers maintenance requirements. The modular design of the YSI system was also a big factor. The stackable modules and single-cable design of the network reduces the wiring required and makes setup convenient. It also greatly simplifies future expansion of the monitoring system. This was important because the Seneca team had plans to expand the system after the initial order to replace other aging monitoring equipment in the facility. The controller display was also superior, as it is larger than competitors’ systems and portable. Anyone can snap a terminal onto any module and it can be programmed to display all sensors in the network or only the sensors physically connected to that particular location.
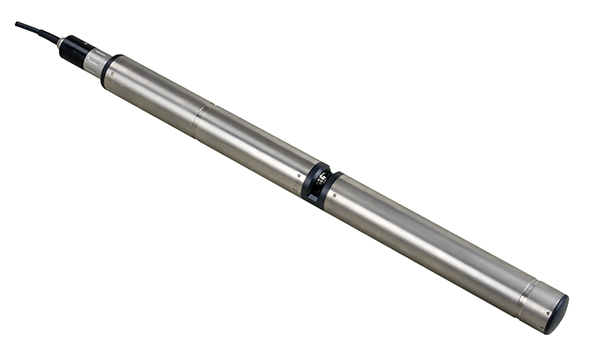
Figure 1. YSI IQ SensorNet NitraVis sensor
The advantages of IQ SensorNet were substantiated but now it was time for a decision to be made on whether to implement it. After all, the current probes were still functional. “Money is always an issue,” says Johnson. “We have to do the best we can, and I had to tell my boss why we wanted the new probes. I told him that this is the most reliable system we have ever used without having to chase them around all the time.” Besides that, the NitraVis (Figures 1 & 2) had 2-for-1 measurement capability which allowed WSSC to also acquire Total Suspended Solids (TSS) on each NitraVis probe, saving $3,000 for a separate TSS probe and adding to the value. Marty’s manager agreed and approved the initial first-stage order for the 2020 controller with 2 NitraVis TSS sensors for 2 of the 5 treatment trains.
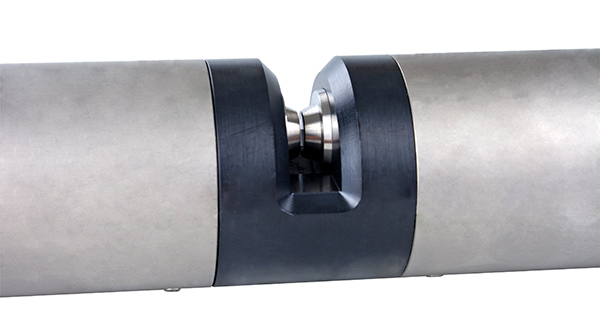
Figure 2. IQ SensorNet UV probes are rugged, accurate and designed to withstand field conditions. The optics are kept clean with UltraClean technology and the sensor's 256-wavelength scan provides unmatched accuracy. A 1-mm gap sensore is pictured.
The IQ SensorNet in Action
The Seneca team quickly set up the YSI system but there was still work ahead for optimization. The monitoring system is an important part of the strategy for efficiently achieving Seneca’s stringent treatment requirements. Integrating the measurements into a stable and efficient control system would be the ultimate goal. The methanol dosing control system, as it was originally conceived, was a feed forward strategy with the probes mounted at the upstream end of the anoxic zone near the methanol dosing point. (Learn more, Wastewater Process Control - Which Strategy is Right for You?). This strategy worked fine most of the time but it was too slow to react to peak loadings with the result that some nitrate bled through the system into the effluent. The nitrate sensors were relocated to the downstream end of the anoxic zone for a feedback control strategy using a nitrate set point of 1.8 to 2.0 mg N/L. It worked. Treatment performance varies over the course of the day but stays within target levels. Effluent TN averaged 1.98 mg N/L over a recent 12 month period with concentrations varying from a minimum of 0.5 mg N/L to a maximum of 5.8 mg N/L.
"There is no drift with the YSI nitrate sensor. I can rely on the measurement."
Maintenance has been simple. The UltraClean system very effectively prevents biofouling. However, a couple of tweaks were made to the system to further reduce operator attention. The position of the vertically-oriented probes was adjusted so that the measurement channel is parallel to the flow to flush solids and debris. In order to clear hair or rags that would occasionally get hung up on the probes and blind the optics, the Seneca Team installed an air cleaning system. The process airline was tapped and an air cleaning valve module (model MIQ/CHV) was added at each probe location. The valve operates at regular intervals to discharge air into the measuring gap to displace debris. The end result is that each probe is removed from the tanks and checked weekly, and manually cleaned monthly.
Share the Wealth
With the success of the initial monitoring system, The Seneca team quickly upgraded their system by replacing the nitrate probes in the remaining 3 ENR trains with IQ SensorNet NitraVis probes. Our FDO dissolved oxygen (DO) probes and SensoLyt oxidation reduction potential (ORP) probes have also been added at the Seneca facility.
Word of the success story was reaching beyond Seneca, too. The largest of the WSSC facilities, Western Branch, consists of 4 treatment trains that operate like 4 separate plants in one. There are a total of 12 aeration basins and 36 clarifiers. As with Seneca, Western Branch was addressing denitrification requirements as part of their ENR upgrades. Dave Kramer, the Chief Plant Operator for the Western Branch, had previously worked alongside Marty and the two of them talk regularly. Marty was happy to share the benefits of the YSI system with Dave and his team.
Furthermore, the Western Branch operations team had some previous experience with a YSI portable DO meter and trusted the brand. But when the Western Branch team started working with IQ SensorNet, and saw the ease of installation, the user-friendly nature of the entire system, and how simple the calibration was – and the fact that the sensors hold their calibration – the Western Branch team ultimately decided to swap out all of their sensors and monitoring/control equipment to the YSI IQ SensorNet network. From ammonia to orthophosphate, and DO to mixed liquor suspended solids (MLSS), the Western Branch facility has been able to take advantage of sensor technology and implement a true monitoring and control system. The IQ SensorNet enabled them to optimize their process, reduce costs, and implement control protocols based on the data they were getting. Hitting their nutrient-reduction numbers has never been easier.
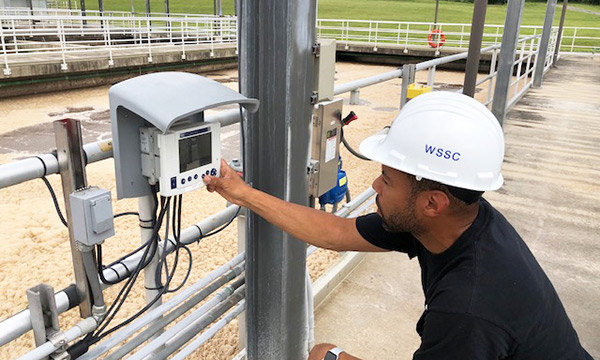
Greg Whitley at the Seneca WRRF using the IQ SensorNet system
Both the Seneca and Western Branch teams have made terrific progress in gaining efficiencies in many areas of their process and it’s certainly a goal they’ve set out to achieve. Meanwhile, the Seneca team continues to seek advancement, focusing on maximizing biological phosphorus removal. IQ SensorNet SensoLyt ORP probes continuously monitor anaerobic zones which promote fermentation and phosphorus release. The Seneca team has discovered that they can drastically reduce alum usage and even realize some energy savings by running mixers intermittently without sacrificing treatment performance. They have achieved effluent concentrations as low as 0.04 mg N/L. This is good news for the Chesapeake Bay and the environment. Improving WSSC discharge numbers ultimately lessens the impact of wastewater treatment on the Chesapeake Bay estuaries - a goal all WSSC facilities have and will continue to have into the future.
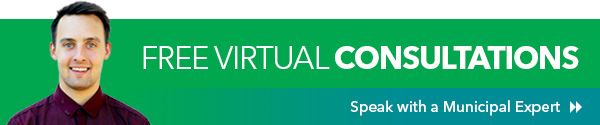
*The Water Environment Federation (WEF; Alexandria, Va.) formally began using the term water resource recovery facility (WRRF), in place of wastewater treatment plant and other conventional names in 2013.
Authored by: Luke Giroux, LGx, LRGiroux Consultants and Dr. Rob Smith, Former Applications Engineer, Wastewater at Xylem, Inc.