Which Wastewater Process Control Strategy is Right for You?
A variety of control strategies, varying in levels of complexity, are currently utilized for process control of activated sludge in wastewater applications. The primary incentives for the control and automation of wastewater treatment plants are compliance with effluent standards and cost reduction. Several control strategies are described below including application, implementation, and advantages and disadvantages.
Manual Wastewater Process Control
Manual operation is the traditional method for wastewater process control. Manual adjustments of control elements are made to maintain parameters within desirable ranges, such as dissolved oxygen.
Early implementation of manual control utilized physical samples and standard laboratory measurements for biochemical oxygen demand (BOD) and total suspended solids (TSS) as the most common sources of data to calculate aggregate parameters including food/microorganism (F/M) ratio and sludge volume index (SVI). This was all well and good because most facilities were only required to meet secondary treatment standards.
Furthermore, wastewater treatment facilities were designed based on hefty safety factors applied to empirical standards for maximum loading conditions. The design priority was meeting discharge permit requirements under any condition not providing flexibility to optimize operation for typical daily loads.
Nevertheless, direct measurements of the process using handheld meters, portable spectrophotometers, and online instrumentation began to be used to supplement standard measurements as the technology became affordable. This enabled better control but there was still a lag between the time the measurements were taken and the adjustment of the control element.
Furthermore, only infrequent adjustments are possible such that the system is never optimized. Despite this major disadvantage, manual operation is still the most common control method today. This is at least partly due to the initial budgetary costs to implement automatic control. However, treatment requirements for nutrient removal, the cost of energy, and the drive for sustainability are providing the incentive for more advanced control in addition to the lower overall cost of ownership.
Automatic Wastewater Process Control
Recent developments in control technology have accelerated the trend towards automatic process control. Multiple levels of automation are now being applied. 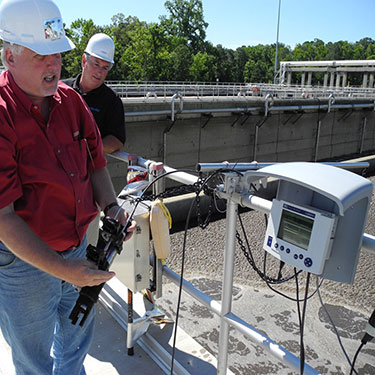
Open Loop Control
The simplest form of automatic process control is open-loop control using a timer. Common implementations of this strategy include intermittent operation of blowers, mixers, and pumps. An attentive operator can observe the effect of manual adjustments on process performance with the aid of manual samplings and measurements and optimize the operating scheme for daily, weekly, and seasonal variations based on a formal or informal set of constraints. This strategy is satisfactory for slow processes or where disturbances are small and predictable such as for a package plant serving an institution. The disadvantage is that adjustments can be made only a few times (or once) per day depending on the availability of the operator and do not closely reflect diurnal variations in wastewater load. The tendency is to adjust the system conservatively as a contingency in case wastewater characteristics change unexpectedly.
Feedback Control
The next level of control is automatic control implemented in SCADA using online measurements. Changing wastewater characteristics cause a disturbance to the process. The disturbance causes a response by the process, a higher or lower dissolved oxygen (DO) concentration, for example, that can be measured. The measurement is reported to a controller which reacts to eliminate the difference between the measurement and the desired setpoint by sending a control signal to an actuator.
The most common and inexpensive form of feedback control is on/off control. The process is controlled using simple relays that start and stop equipment in response to a disturbance. Another benefit is that on/off control can be retrofitted into existing facilities with minimal modifications. The typical application is in batch or semi-batch processes such as blower control for cyclic activated sludge-based on online measurements of DO. The main drawbacks are process instability and actuator wear as a result of oscillation above and below the setpoint.
At high loadings, airflow has to be started and stopped frequently because the dissolved oxygen falls rapidly once the setpoint is reached causing wear on the actuator. As loadings decline, a small burst of air causes the dissolved oxygen to overshoot and persist above the setpoint. Dead band and hysteresis can be applied to minimize oscillations but then the process control system is more complex.
More efficient control of wastewater aeration requires a proportional-integral-derivative (PID) controller to maintain the process closer to setpoints and more closely match the responses to the demand. For example, the standard configuration for a DO control system utilizing a PID loop is a cascaded control system. The DO controller calculates the airflow required based on the difference between the input DO setpoint and online DO sensor measurement.
The output from the DO controller (the master) is the setpoint for the airflow controller (the slave) which compares the airflow setpoint with the actual airflow and adjusts the basin or zone airflow control accordingly. The drawbacks to feedback control are that response can only occur after the disturbance has occurred, tuning the system to match large and/or frequent disturbances is complex, and it is not possible if the response variable cannot be reliably measured.
Feed Forward Control
Feed forward control consists of measuring the disturbance and calculating the required response. A common implementation of this strategy is an extension of cascade control for feedback control based on DO. An ammonium controller sits on top of the DO controller and receives input from online instruments measuring flow and ammonium, calculates the load, and determines the DO setpoint. The benefit is that suppression of DO and bleed-through of ammonia into the effluent can be eliminated because the controller anticipates the aeration demand instead of reacting. The drawback is that it requires additional sensors to measure ammonium and a model to calculate the response based on the disturbance. A feedback loop may also be needed to adjust the model-predicted response.
Regardless of your wastewater facilities' level of control, YSI has instrumentation for the field (Optical DO), laboratory (BOD, pH, etc.), and continuous online process control instrumentation (IQ SensorNet).
Learn more about IQ SensorNet and earn CEU's at our Wastewater On-Demand Learning page.
Additional Blog Posts of Interest:
Troubleshooting Nitrification and Denitrification in Wastewater
ORP Management in Wastewater as an Indicator of Process Efficiency
Myths and Realities: Ammonium Based Aeration Control in Wastewater
Shortcut the Nitrogen Removal Process in Wastewater with UV Sensors