Wastewater Process Efficiency Using ORP Management
Oxidation-reduction potential, or ORP (redox), has been used for many years in facilities that process wastewater generated by metal finishing plants, but recently it has become prominent in municipal wastewater treatment plants.
When using a typical ORP device, an operator inserts a probe directly into a plant’s tank or waste stream. The probe contains a sensor that measures electrical charges from particles, called ions, and these charges are converted to millivolts (mV) that can be either negatively or positively charged. Unlike “wet Chemistry” analysis that can be time-consuming and complex, ORP readings are instantaneous and easy to perform. And like all sampling measurements taken by operators, they are snapshots in time that can indicate process efficiency and identify treatment problems before they affect effluent quality. When using continuous monitoring and control instrumentation, this snapshot can become a real-time indicator.
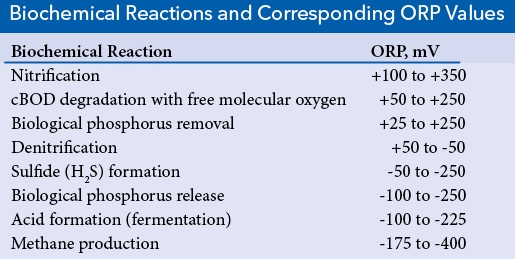
When used in wastewater treatment systems, oxidation-reduction potential is a measurement of the ability or potential of wastewater to permit the occurrence of specific biological (oxidation-reduction) reactions. Important oxidation-reduction reactions in wastewater treatment systems include nitrification, denitrification, biological phosphorus removal, biological malodor production, and the removal of cBOD (carbon- and hydrogen- containing compounds). These reactions involve carbon (C), phosphorus (P), sulfur (S), and nitrogen (N) and their change from oxidized states (containing oxygen) such as nitrate (NO3-) and sulfate (SO42-) and reduced states (containing hydrogen) such as ammonia (NH3) and sulfides (H2S).
ORP is measured in millivolts (mV) and on the ORP scale, the presence of an oxidizing agent such as oxygen increases the ORP value, while the presence of a reducing agent such as substrate or cBOD decreases the ORP value.
By monitoring the ORP of wastewater, an operator can determine what biological reaction is occurring and if operational conditions should be changed to promote or prevent that reaction.
For example, an operator doesn’t want denitrification or “clumping” to occur in a secondary clarifier; the operator, therefore, must maintain an ORP value of more than +50 mV to prevent clumping. Similarly, an operator doesn’t want malodor production to occur in the sewer system. So, the operator must maintain an ORP value of more than -50 mV to prevent sulfide formation and an ORP value of more than -100 mV to prevent volatile acid formation.
Let’s take a look at each of these reactions and their relation to ORP values in greater detail.
Nitrification
To satisfy discharge limits for total nitrogen or ammonia, wastewater treatment plants must nitrify. Nitrification is the oxidation of ionized ammonia (NH4+) to nitrate (NO3-) and is performed by nitrifying bacteria when the ORP of the wastewater is +100 to +350 mV.
Denitrification
Denitrification is performed to satisfy total nitrogen discharge limits or destroy undesired filamentous organism growth. Denitrification is the reduction of nitrate (NO3-) to molecular nitrogen (N2) and is performed by denitrifying bacteria when ORP of the wastewater is +50 to -50 mV.
Biological Phosphorus Removal
Wastewater plants conduct biological phosphorus removal to meet total phosphorus discharge limits. The process consists of two treatment steps - first, biological phosphorus release and, second, biological phosphorus removal.
In biological phosphorus release, fermentative bacteria produce fatty acids in an anaerobic tank having an ORP range of -100 to -225 mV. When the acids are absorbed by phosphorus-accumulating bacteria, the bacteria release phosphorus to the bulk solution.
In the second step - biological phosphorus removal - the phosphorus-accumulating bacteria degrade the absorbed acids in an aerobic tank and store the energy that was obtained from the degraded acids in phosphorus granules. This storage of energy requires the removal of large quantities of phosphorus from the bulk solution. The storage of phosphorus granules or biological phosphorus removal occurs when the ORP of the aerobic tank is +25 to +250 mV.
Sulfide Formation and Fermentation (Biological Malodor Production)
Biological malodor production occurs through two major biochemical reactions, sulfide (-SH) formation and acid formation (fermentation). Hydrogen sulfide is produced in large quantity when sulfate-reducing bacteria degrade substrate using sulfate (SO42-). Sulfate is found in groundwater and urine and when reduced through bacterial activity, hydrogen sulfide (H2S) is formed.
Sulfide formation, which occurs when the ORP is between -50 to -250 mV, is a critical event in an anaerobic digester, where the sulfide serves as a sulfur nutrient for facultative anaerobic and anaerobic bacteria including the methane-producing bacteria.
During the equally critical event of fermentation, acid-forming or fermentative bacteria produce a large variety of volatile acids, nitrogen-containing compounds, and sulfur-containing compounds. Many of these volatile compounds are malodorous. Acid formation or fermentation occurs when the ORP is between -100 and -225 mV. Fermentation is particularly crucial in biological phosphorus removal systems where the production of fatty acids is required for phosphorus release. Fermentation is also important in anaerobic digesters where many of the acids and alcohols produced through fermentation are used by methane-forming bacteria to produce methane.
However, these reactions must be appropriately confined. Septic conditions that permit sulfide formation and the discharge of sulfide into an activated sludge process should be corrected. The presence of sulfide promotes the growth of undesirable sulfide-loving filamentous organisms such as Beggiatoa spp., Thiothrix spp., and type 021N.
cBOD Degradation with Free Molecular Oxygen
Removal or degradation of cBOD with free molecular oxygen (O2) occurs when the ORP in the reaction tank or aeration tank is between +50 to +250 mV. The degradation is performed by cBOD-removing bacteria. The bacteria are aerobes (using only free molecular oxygen) or facultative anaerobes (using free molecular oxygen or another molecule such as nitrate).
Methane Production
Methane (CH4) production is highly desired in an anaerobic digester and undesired in a sewer system. Methane production is performed by methane-forming bacteria and occurs over a large range of ORP values, from -175 to -400 mV.
Knowing the ORP values associated with specific reactions has allowed operators to use ORP probes, and the information gleaned from them, in a variety of helpful ways. Within a sewer system, for example, an ORP value less than -100 mV indicates the production of malodors due to sulfide formation and fatty acid production. By adding sodium nitrate (Na2NO3) to a manhole, it’s possible to increase the ORP value above -50 mV and prevent biological malodor production.
In another example, the transfer of thickener sludge that is heavily laden with nitrate to an anaerobic digester may be regulated by monitoring the ORP of the digester sludge. As the ORP increases from -400 mV, the transfer of thickener sludge may be terminated at a value less than -300 mV to prevent the loss of significant methane production.
Consider too that the absence of denitrification within a denitrification tank may be detected with the use of ORP and hydraulic retention time of the tank or cBOD feed (methanol or acetate) to the tank may be adjusted to promote denitrification. Likewise, the occurrence of biological phosphorus release may be monitored in a fermentative tank and if needed, hydraulic retention time may be increased in order to remove residual free molecular oxygen and nitrate that contribute to ORP values of more than -100 mV.
ORP probes are extremely versatile measurement systems for monitoring biological reactions within sewer systems and wastewater treatment plants, and for indicating to operators if an acceptable or unacceptable biological activity is occurring. Increasingly, they are a tool that wastewater treatment plants must have and that operators must know how to use.
The following article is reprinted with the permission of the New England Interstate Water Pollution Control Commission (NEIWPCC). It was written by Michael H. Gerardi, and appeared in the Winter 2007 issue of NEIWPCC’s newsletter, Interstate Water Report. To view the original, please visit, www.neiwpcc.org/iwr/reductionpotential.asp.
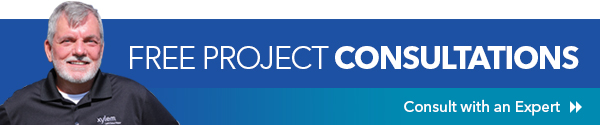
Additional Blog Posts of Interest:
Solving Water Resource Recovery Issues with Monitoring and Control
Can Smart Devices Enhance Water Resource Recovery Facilities?
Myths and Realities: Ammonium Based Aeration Control in Wastewater
Wastewater Process Control - Which Strategy is Right for You?