Contact Water Level Sensors
These types of sensors have been around the longest. There is a wide range of contact sensors – from incredibly simple to high-tech – and some are designed for specific applications.
Crest Stage Gages
A crest-stage gage is a simple way to measure water level, most often in streams and rivers. These gages consist of a metal pipe, wood staff, and a cork that’s been crushed up. Unlike modern level sensors, the crest-stage gage can only record the maximum water level. They are typically ‘reset’ before a high-water event occurs and checked by a technician after the event is over or when the water level has stopped rising.15
Water enters through holes in the bottom of the pipe. It rises in the pipe, with the cork floating on top. Once the level stops rising, the cork sticks to the wood staff, and it stays there while the water recedes.15
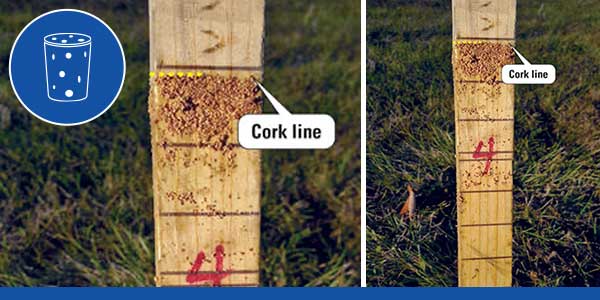
Crest-Stage gages use crushed cork and a wood staff to record the maximum water level.15
Besides only being useful during high-water events, there are several potential issues with the design of a crest-stage gage:
- The holes in the bottom of the metal pipe can become clogged.
- Ants can build nests on the cork, thus preventing it from rising once a flood occurs.
- The cork can get washed out of the vent hole.
Staff Gages
A staff gage provides a visual indication of the current water level. It looks like a ruler and is attached to a static structure, such as a bridge. The gage can be installed vertically or flush with the streambank on an incline, as this helps prevent damage.16 Staff gages are one of the most common reference sensors used when calibrating electronic level sensors.
Staff gages are appropriate for water level measurement in nearly any application (e.g., rivers, reservoirs, wetlands). They do have limitations, as there’s no way to monitor staff gages remotely – someone has to be on-site collecting data.
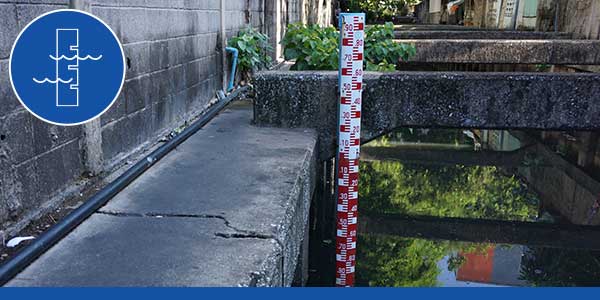
Staff gages look like giant rulers that are used to measure water level. This image is from a canal in Din Daeng District, Bangkok, Thailand. Staff gages are one of the most basic water level indicators in use today.
Wire-Weight Gages
There are different flavors of wire-weight gages, but they all operate similarly. Wire-weight gages are placed over a body of water and are often attached to a bridge handrail. They consist of a drum wound with a cable that has a weight at the end. The technician lowers the weight to the surface of the water using a crank. A counter is part of the gage, and it is what determines how far the weight has been lowered. Once the technician has recorded a reading, they crank the cable back up from the water's surface.16 Like staff gages, wire-weight gages are often used as a reference when calibrating electronic level sensors.
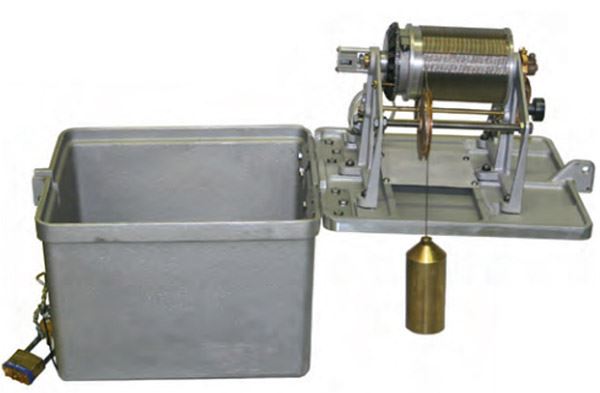
Wire-weight gages are often attached to a bridge. The technician lowers the weight to the water's surface to get a level measurement. This image is from the USGS manual on Stage Measurement at Gaging Stations.
Wire-weight gages have a simple design, but they can be challenging to use. In turbulent conditions, multiple readings will be needed to determine the water level. If the water is still, it can be difficult to tell when the weight is touching the water.16 Like crest-stage and staff gages, wire-weight gages require a technician to visit the site and record measurements.
Float Switches
A float switch – sometimes referred to as a level switch – indicates when the water level has risen or fallen to a specific point. These level sensors are most commonly used inside tanks at wastewater facilities and often trigger pumps or alarms. Because they are often deployed in harsh environments, float switches are constructed with rugged materials such as polypropylene.
All Xylem float switches operate on the same basic principle – any change in position causes the sensor to activate.
Shaft Encoders
Shaft encoders are used to measure level in a stilling well as part of a streamgage station, hydrometeorological site, or flood warning system. However, they are also sometimes used in groundwater wells.
Stilling wells are large vertical structures with a hollow center – many look like a giant tube – and are often installed along a riverbank. Water enters through pipes at the bottom of the well; this allows the water level in the well to be the same as that of the river.17 This design protects instrumentation inside the well and mitigates the impact of wind and turbulence on water level.16
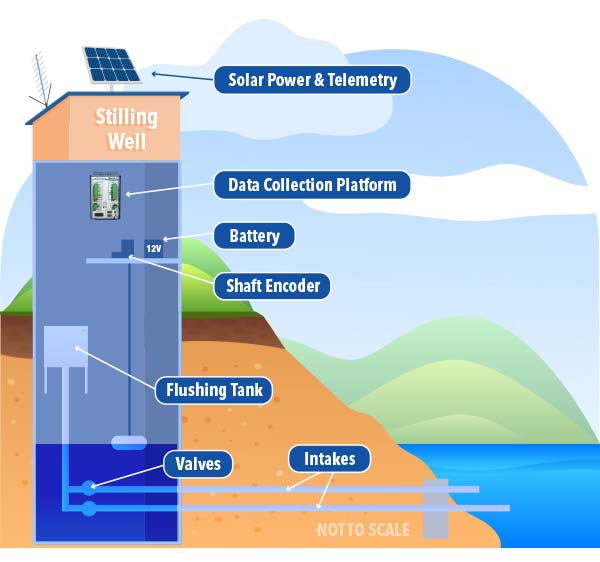
Shaft encoders must be installed in a stilling well. Despite having a relatively simple design, shaft encoders can transmit real-time data when coupled with a datalogger and data transmitter. This graphic is adapted from an image in the USGS manual on Stage Measurement at Gaging Stations.
The YSI Shaft Encoder features a box with an internal microprocessor-controlled digital counter, a shaft, a pulley, and a weight with a float that hangs from the pulley. As the water level changes, the encoder’s shaft rotates. This change in position is translated into a change in level by the shaft encoder.
Shaft encoders are simple, accurate, reliable, and inexpensive. However, they must be installed inside a stilling well. Not only is a stilling well expensive and time-consuming to install, but they also have maintenance requirements and can be unsafe for those that need to service them.
Submersible Pressure Transducers
Submersible pressure transducers measure level by calculating the pressure exerted on them from the water column above – the more water above the sensor, the greater the pressure. Pressure is then converted to either feet or meters.
Another source of pressure picked up by the sensor is the pressure exerted by the atmosphere upon the water’s surface. Therefore, barometric pressure is a significant variable to consider when using pressure transducers. In general, there are two types of submersible pressure transducers – absolute and differential – that differ in how they handle barometric pressure compensation.
So, how are absolute and differential level sensors different? Differential pressure transducers are vented to the air via a vent tube, allowing the overall measurement to be compensated for barometric pressure. Examples of differential sensors include the WL450 pressure transducer and the EXO1/EXO2 multiparameter sondes with the vented option.
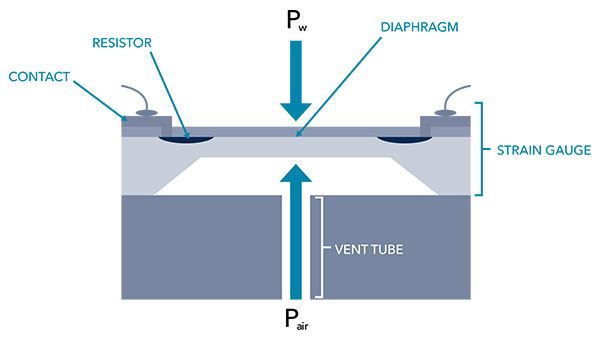
Differential sensors are vented to the air via a vent tube. This enables the overall measurement to be automatically compensated for barometric pressure.
In contrast, absolute pressure transducers are not vented, so the pressure reading from the transducer reflects both the barometric pressure and the pressure attributed to the water column above it. Data can be adjusted to remove the influence of barometric pressure if an external barometric pressure sensor is used, but this requires additional steps. This also decreases the overall accuracy, as the error attributed to both the water level sensor and barometric pressure sensor are present in the final measurement.
Examples of absolute pressure transducers (i.e., non-vented sensors) include the EXO1/EXO2 multiparameter sondes without the vented option. The ProDSS and ProSwap systems with an optional depth sensor are unique, as they measure virtual vented depth. The virtual vented depth measurement allows for real-time compensation for atmospheric pressure using the handheld’s built-in barometer.
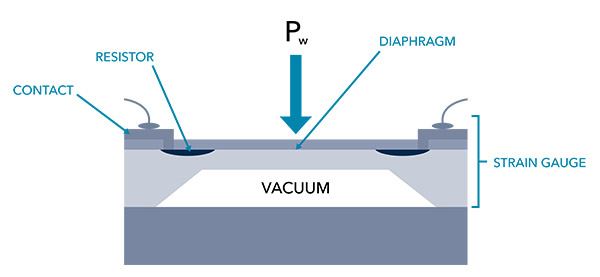
Diagram of a non-vented pressure transducer, also called absolute pressure transducers. One side of the sensor’s diaphragm is exposed to the water – where pressure changes – and the other side is exposed to a vacuum – where pressure is constant.
Check out our blog on Groundwater Measurements at High Altitude to learn more about these types of level sensors and the impact of barometric pressure on level data.
Submersible pressure transducers can be used in a variety of applications, although they are most often used in groundwater. They are typically used in conjunction with a datalogger and a telemetry device when continuously monitoring water levels.
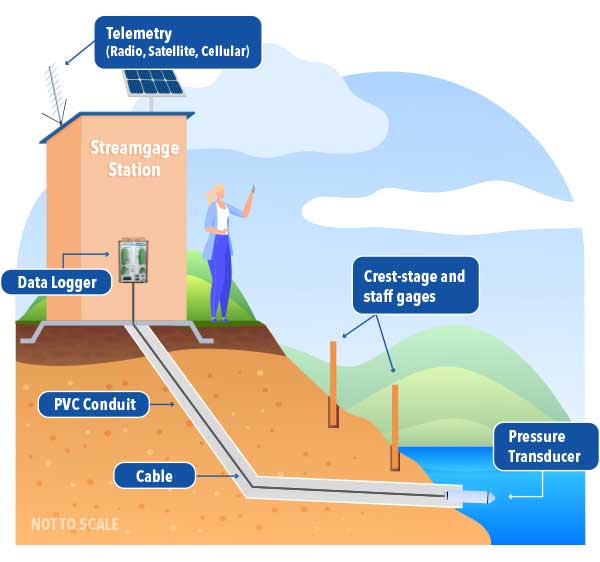
When submersible pressure transducers are used in surface water applications, they are often coupled with another water level indicator that serves as a reference gage; a staff gage is commonly used.
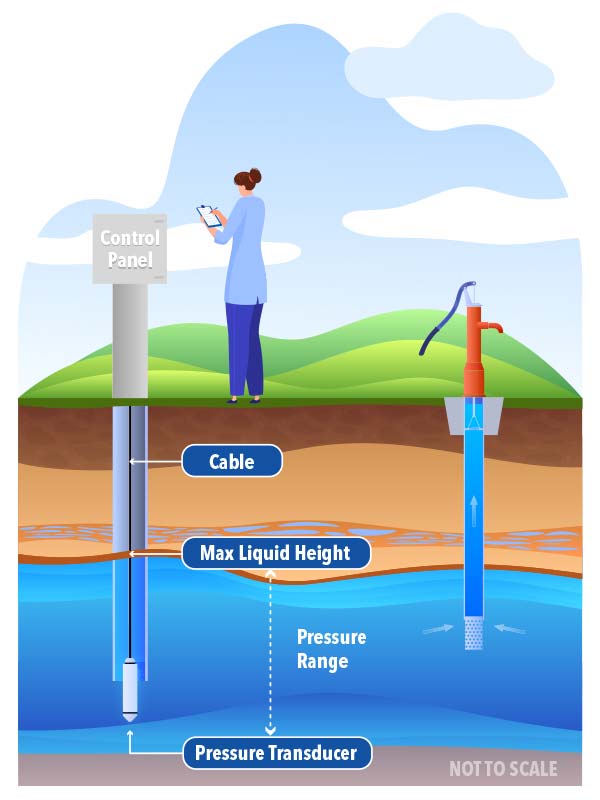
Submersible pressure transducers are commonly used in groundwater applications. This image shows how the level sensor is placed in a well.
Submersible pressure transducers are easy to use. However, the sensing portion of the instrument – electronics included – is placed in the water, so they have a shorter lifespan than some other sensors (e.g., Bubbler or Radar). Also, pressure transducers can become clogged or damaged by debris in the water column are not the best choice when the water is turbulent.
Bubblers
Bubblers feature pressure sensors that are not placed in the water. However, they are still considered contact sensors, as part of the instrument – the orifice line (e.g., a plastic tube) – is placed in the stream.
Instruments like the Amazon Bubbler operate by continuously forcing air from the instrument housing through the orifice line. A pressure sensor in the instrument housing records the pressure required to push the air out of the line, while an onboard barometer automatically compensates measurements for barometric pressure.
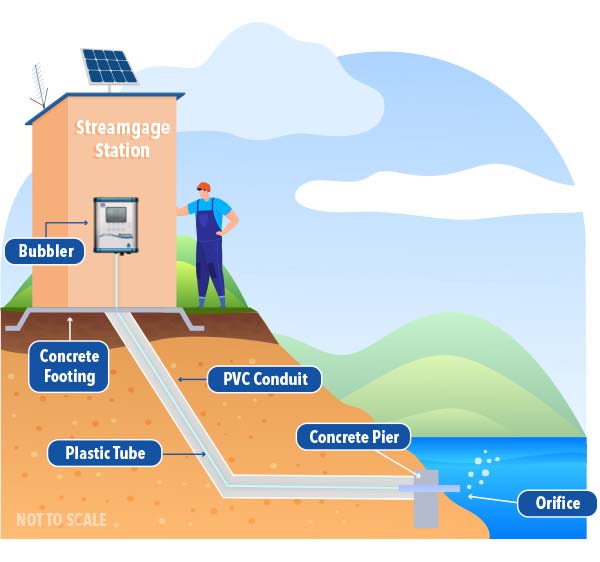
A bubbler can be used to determine gage height. The instrument housing is placed in an enclosure (e.g., a streamgage station). The orifice line is fed through a conduit, and it goes from the instrument to the water. The end of the orifice line must be secured in place to ensure accurate data is collected.
Bubblers are accurate and can be used in a variety of applications, although they are most often used in surface water. The sensor is not placed in the water column, thus reducing the risk of premature sensor failure and damage to the sensor from debris. Therefore, bubblers tend to last longer than submersible pressure transducers. There are very few drawbacks to bubblers, one of which is the potential for the orifice line to become clogged.
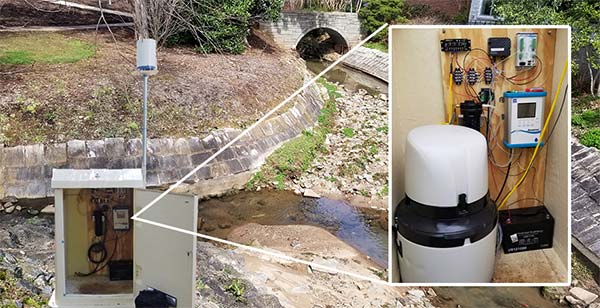
A continuous water monitoring station could include a bubbler water level sensor such as the Amazon Bubbler, EXO multiparameter water quality sonde, Storm 3 Datalogger, and ProSample sampler. Read more about a setup like this in our application note on Determining the Source of Stream Toxins.
Acoustic Sensors
Instruments like the SonTek-IQ and SonTek-SL use an acoustic beam to measure water level. The beam sends a short pulse and waits for a reflection from the water’s surface. The instrument converts the reflection time to level based on the speed of sound in the water at the site; this depends on temperature (measured with an integrated sensor) and salinity (user-defined).
While the beam is the primary measurement method, an onboard pressure sensor serves as a secondary measurement in the event valid data from the acoustic beam cannot be collected. The pressure sensor is not vented to the atmosphere; therefore, it must be calibrated for changes in atmospheric conditions.
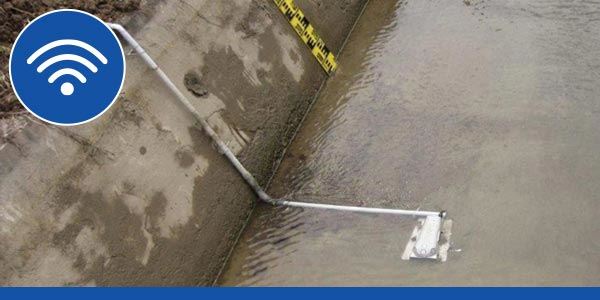
In this image, a SonTek-IQ measures velocity and stage in an open channel in Italy.
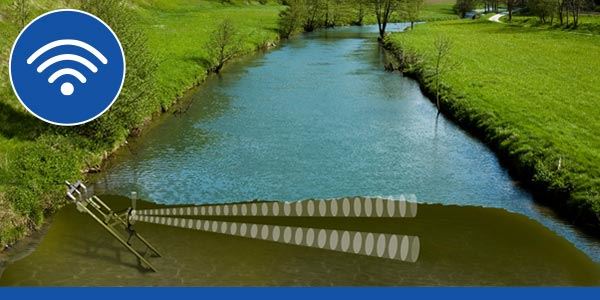
The SonTek-SL, affectionately known as the Side-Looker or "S.L.," is designed specifically for side mounting on bridges, canal walls, or riverbanks.
The main advantage of instruments like the SonTek-IQ and SonTek-SL is they measure velocity in addition to level. The SonTek-IQ is ideal for monitoring flows in canals, culverts, pipes, and natural streams. The SonTek-SL is designed for side mounting on bridges, canal walls, or riverbanks, making it ideal for coastal areas, ports, rivers, and irrigation.
The primary disadvantage to acoustic instruments is cost; these are the most expensive type of level instruments. Also, they are susceptible to fouling covering the sensing surfaces and can be complex to maintain. Thus for the purpose of measuring level alone, acoustic sensors might not be the best choice. But if level is the secondary aim and flow is a priority, these sensors can't be beat.