Wastewater or Water Resource Recovery Facility?
The term ‘wastewater’ is a misnomer. It is more accurate to call it - water dispensed from a tap and used for drinking, hygiene, recreation, and industrial uses, and then returned through the drain - resource water because of all the useful embedded resources.
For example, researchers have calculated the potential for energy generation from wastewater is 5 times the amount of energy required to treat it. Thus wastewater treatment is being re-branded water resource recovery. Conversely, many other resources are wasted by the inefficient design and operating practices that are currently used for extracting water from and returning water to, the environment. Water resource recovery, in particular, has a large carbon footprint, consuming 0.6% of total energy generation in the US.
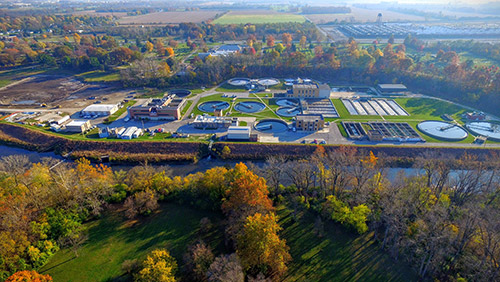
The 24 MGD Muncie activated sludge wastewater treatment plant serves a population of approximately 31,000.
Aeration Technology
Aeration is a critical component of water resource recovery facilities (WRRF). It delivers life-sustaining oxygen to the consortium of microorganisms which perform the bulk of work transforming pollution into harmless end products and it keeps those microorganisms mixed with the water being treated. In the most common configuration, the activated sludge process (ASP), aeration entails pumping air into basins known as aeration tanks filled with microorganisms suspended in water, known as mixed liquor suspended solids (MLSS). The process is very energy-intensive due to physical limitations associated with dissolving oxygen into water and operational challenges with balancing the rate of aeration with oxygen demand. (Learn more, How to Control Activated Sludge with Online Sensors).
The air (oxygen) supply system consists of large machines called blowers that pump ambient air into the aeration tanks through a distribution system of diffusers, disks, or panels with holes in them, mounted on the bottom of the aeration tank. Blower and diffuser technology have both improved markedly during the past 10 years improving the potential for energy usage reduction. Furthermore, improved technology for online process monitoring has made automation of the aeration process more achievable allowing utilities to balance the air supply rate with the oxygen demand which changes as water and waste generation varies daily, weekly, and seasonally. It is the mixing requirement, however, which dictates the aeration rate for many utilities in the Midwest with aging and outdated infrastructure. (Learn more, Controlling Aeration Costs in Wastewater Treatment Facilities with Online Measurements).
Achieving Energy and Cost Savings
Energy is also wasted treating a lot of water which doesn’t require treatment in the first place. Combined sanitary and storm sewer systems were common practice in the early 20th century when communities in the Midwest were first being sewered. The main objective was to chase water downstream away from urban areas to prevent diseases. Treatment was an afterthought. Many of these combined systems are still in service. In addition, infiltration and inflow (I&I) from groundwater, storm water, and sometimes even river water, gets into the sanitary sewer system through cracks in the sanitary sewers and cross-connections with storm sewers.
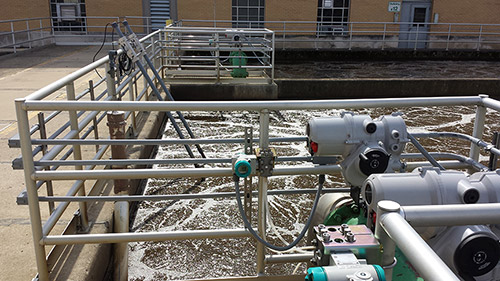
To support real-time monitoring and control, YSI IQ SensorNet sensors were installed in the basins.
Building foundation drains allow even more clean water into the sanitary sewer. Energy is wasted pumping the clean water to the WRRF, and, once it is there, pumping it around and treating it.
Furthermore, clean water complicates automatic control of aeration because it dilutes the waste requiring more aeration tanks to be in operation, such that, the mixing requirement dictates aeration operation instead of oxygen demand. Continuous aeration is a very inefficient method of mixing but it is the limiting factor for many facilities. This was the exact challenge faced by the Muncie Sanitary District (MSD) in Indiana. An innovative system of automated DO control and a sequenced pulsed aeration mode of operation has allowed it to optimize aeration and save more energy and money than traditional solutions could achieve.
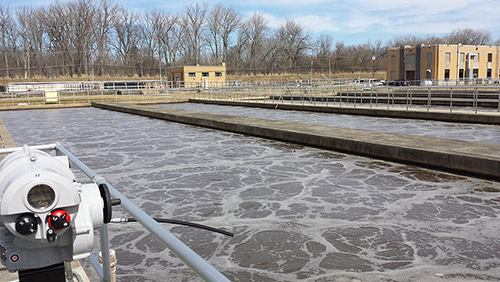
Under the sequenced pulsed aeration mode of operation, the aeration system now runs at lower DO levels, reducing energy use.
Process Monitoring & Control
The Muncie Water Pollution Control Facility (WPCF) is the WRRF for a population of approximately 31,000 people generating an average of 24 million gallons of used water per day (MGD). The system was constructed and modified in stages beginning in 1941. The activated sludge aeration system consisted of four aeration basins and approximately 9,000 ceramic fine bubble aeration diffusers which distribute air supplied by three 500-hp constant speed blowers. Online dissolved oxygen (DO) probes were installed in the aeration basins but the readings were displayed only and not used to automate aeration.
Instead, Muncie utilized a version of ‘SneakerNet’, walking out to observe the online DO readings and then walking to the control valves to make manual adjustments and then walking back to the probes to check if the adjustments had the desired effects on the DO readings. John Barlow, Muncie WPCF Superintendent, explains. “Our operators would have to turn up the blowers by hand and then adjust the individual header valves. But, by the time the afternoon shift came on, the DOs would start climbing and operators would have to again turn the blowers down and readjust the header valves.” Ultimately, Barlow decided to stop manually adjusting the aeration valves and run the system at a high rate all day.
He explains, “I decided to run the blowers higher because maintaining the needs of the bacteria is our primary goal, plus running our operators around all day turning blowers up and down and adjusting header vales was an inefficient use of manpower. In addition, the quality of our final treated effluent would become inconsistent with all the roller coaster action of trying to maintain optimum DOs under our process conditions.” The facility maintained an excessively high aeration rate until it upgraded and automated its aeration system as part of a major plant upgrade.
The upgrade of the existing aeration system included an energy-efficient turbo blower, membrane disc aeration diffusers, and an automated control system. The replacement 350-hp turbo blower replaced an existing 500-hp centrifugal blower to provide a more efficient method for supplying air, consuming 10 to 20% less energy. Six-thousand of the ceramic air diffusers were replaced with Xylem Sanitaire Silver Series II membrane disc diffusers for a fine and uniform bubble pattern for oxygen transfer. The remaining 3,000 ceramic diffusers were removed or plugged off.
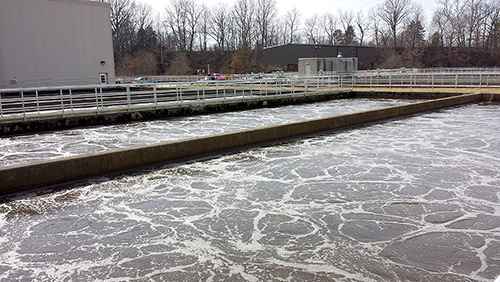
By adopting automated aeration control, the Muncie Water Pollution Control Facility now has the ability to vary the oxygen supplied to meet changes in flow and BOD loading, bringing energy efficiency and improved performance to its activated sludge process.
The new automation system consisted of a Xylem Sanitaire OSCAR process performance optimizer aeration control system including a programmable logic controller (PLC), a YSI IQ SensorNet (IQSN) process monitoring system, and a graphical human machine interface (HMI) which displays status of the aeration system and provides a means to make adjustments. The process monitoring system included 12 model FDO 700 calibration-free optical DO probes and 4 model VARiON 700 ion selective electrode (ISE)- style ammonium and nitrate combination probes. The DO and VARiON probes are continuously read by the control system which automatically adjusts blower output based on current DO readings and water flow. The OSCAR™ control system integrates into the plant’s existing control system and displays the probe readings and system status through its built-in human machine interface (HMI).
True Cost Savings
The new equipment has achieved the energy savings goals but not the way that was expected. The project was originally conceived with an ammonia-based aeration control strategy. The discovery that the system was nearly continuously mixing limited due to an underloaded condition meant that DO levels remained well above targets; there was no opportunity to reduce aeration based on online ammonium measurements with the aeration system as it was designed.
Instead, Xylem Sanitaire designers conceived an alternative method to reduce the aeration rate and still achieve mixing requirements. After a short trial in one basin proved successful, a sequence of aeration pulses was programmed into the control system, allowing the air supply rate to be reduced significantly (the majority of the time) while maintaining the MLSS in suspension with intermittent pulses of aeration at a higher rate. Under the sequenced-pulsed aeration mode of operation, the aeration system now runs at lower DO levels, the majority of the time.
“We initially struggled to have our DO levels close to where we wanted them to be but still get enough mixing, but our controller’s new pulse program took care of that,” Barlow says. The ammonium probes are working well for monitoring but are not part of the automatic control system.
The aeration upgrade and innovative solution for satisfying mixing requirements has allowed MSD to get some of the ‘waste’ out of water.
Barlow states, “We now save more than $5,000 per month with the new aeration system, and that’s with a low rate for electricity. For 2014, the plant consumed more than 640,000 kilowatt hours and in 2016 it was just over 500,000 kilowatt hours.“
Besides power efficiency, Barlow says there’s a lot more efficient use of staff by having more precise aeration control. “From an operations standpoint, if our operators want to change DOs, they no longer have to manually turn blowers and then adjust 12 different header valves because now it’s all automated. The operations manager can increase or decrease the duration between pulses very easily. It’s a very flexible system.“
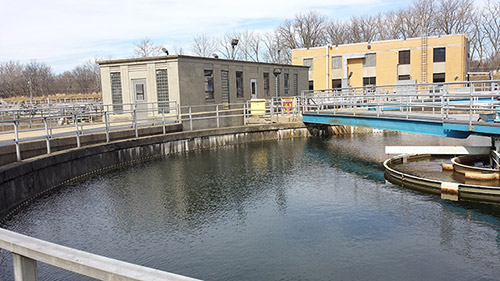
The City of Muncie Wastewater Treatment Plant operates more efficiently.
Furthermore, the facility gets more nitrogen out of the water. At the front end of the aeration basin, where oxygen demand is highest, the DO concentration remains close to zero in what is called an aeratedanoxic condition which facilitates removal of nitrogen. The direct benefit is a further reduction of the energy requirement for aeration by cultivating facultative organisms which require less dissolved oxygen for survival. An important benefit to the watershed and Mississippi River basin is that less nutrients are available to support excessive algal growth downstream, which includes the Gulf of Mexico where the input of nutrients from upstream sources has lead to a hypoxic dead zone.
Fundamental to energy efficiency and optimal performance of any activated sludge process is the ability to vary the aeration rate to meet variable flow and load conditions. This is a challenge for many WRRFs. But through automation and taking the novel approach of adopting a sequenced-pulsed aeration mode, the Muncie WPCF has met this challenge, matching aeration to loading, providing stable effluent quality in compliance with discharge limits, and at a substantial energy savings.
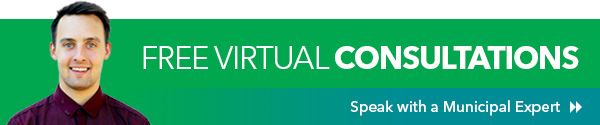
Additional Blog Posts of Interest
How Automated Orthophosphate Monitoring Cut Costs by 25 Percent
Operational Efficiency with SCADA and Continious Process Monitoring
Activated Sludge | three Ways to Improve Your Process Efficiency
Water Reclamation Facility Meets Discharge Limits for Total Inorganic Nitrogen