Cut Costs by 25 Percent with Orthophosphate Monitoring
An automated system for monitoring orthophosphate and regulating chemical feed gives the staff of the Watertown, Wisconsin Wastewater Treatment Plant (WWTP) peace of mind and saves the city between $25,000 and $40,000 per year in ferric chloride costs.
The Operators work hard to maintain monthly average effluent Total Phosphorus (TP) levels below 1.0 mg P/L in accordance with a total maximum daily load (TMDL) for the Rock River. Some phosphorus removal occurs in all activated sludge facilities—approximately 1 mg P/L is removed for every 100 mg BOD/L that is removed due to normal biomass growth and is discarded when sludge is wasted. An extra boost is needed, however, to achieve the necessary effluent quality at Watertown WWTP.
Watertown WWTP staff members utilize a chemical booster, ferric chloride, which is added to mixed liquor upstream from the final settling tanks. The chemical reactions that occur when ferric chloride is added to mixed liquor are complicated, involving both fast and slow reactions. Ultimately, dissolved phosphate is converted to particulate phosphorus. In this method, known as simultaneous precipitation, the particulate phosphorus co-precipitates with mixed liquor and is removed with waste-activated sludge (WAS) as shown in Figure 1.
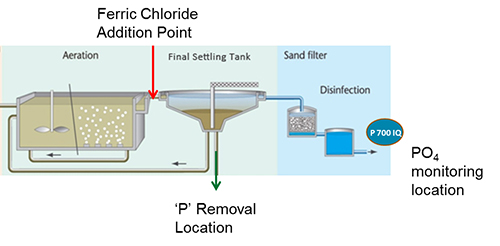
Figure 1 - Typical Simultaneous Precipitation ‘P’ Removal System Configuration
Prior to continuously monitoring the Watertown system, plant operators played it safe with conservatively large dosages of ferric chloride to ensure that TP levels would remain below the prescribed limit.
“The guys would take orthophosphate readings in the morning and afternoon and bump the ferric chloride levels up if the phosphate levels were high,” recalls Kevin Freber, Water Systems Manager for the City of Watertown. “Basically, they were guessing at the right amount to feed into the mixed liquor.”
“If the reading was still high, or higher, in the afternoon, they’d jack up to the next feed rate,” he adds. “It would run like that for seven or eight hours until the next morning. They’d finish up for the weekend and leave it cranked up.”
In many cases, the result was a steady over-application of ferric chloride. “It wasn’t their fault,” Freber notes. “They just didn’t have the right tools to make good decisions.”
Continuous Orthophosphate Monitoring
In 2012, Freber and his team installed their first automated orthophosphate analyzer in the plant, which is designed for 5.2 million-gallon-per-day (MGD) flow but handles an average daily flow of 3.0 MGD. The instrument—a first-generation orthophosphate analyzer by WTW, a Xylem brand—took measurements of orthophosphate every 15 minutes in secondary effluent upstream from the UV purification system. It then automatically adjusted the ferric chloride feed pumps to regulate chemical input rates based on a 0.7 mg P/L setpoint.
“Before we installed the first orthophosphate analyzer, we spent over $100,000 on ferric chloride per year,” says Freber. “After the first year with the analyzer, we saved $25,000, enough to pay for the unit. We’ve been running right about $60,000 to $75,000 a year for ferric chloride since then.” Plant staff also realized other benefits, such as reduced sludge production, further reducing operating costs for sludge disposal.
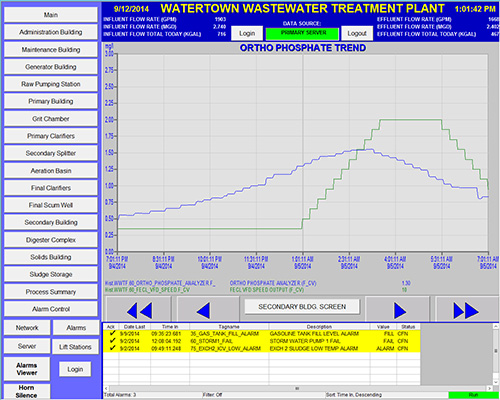
Figure 2 - Phosphorus Removal System Monitoring and Control System Operation
In 2015, Freber worked with Mulcahy Shaw Water of Cedarburg, Wisconsin, to upgrade to a new IQ SensorNet P700 IQ orthophosphate analyzer manufactured by YSI (Request Pricing), which is also a Xylem brand.
The new P700 IQ dramatically reduced reagent costs and lengthened the solution exchange interval to every four to eight months. Among the increased capabilities of the new instrument was its wide measuring range of 0.05 to 50.00 mg P/L. The broad detection capability provides plant designers and management with the flexibility to site the monitoring system and the ferric chloride input in a variety of places within the treatment system.
Ferric chloride or alum may be added to wastewater upstream or downstream from the biological processes, depending on whether plant staff wants to remove the phosphorus with the primary sludge or waste activated sludge (WAS). It can be removed in the primary settling tanks, final settling tanks or effluent filters. Once they’ve decided where the precipitation of phosphorus will take place, they can decide where to install the monitoring system. Most of our customers choose to remove phosphorus with the WAS and locate the P700 IQ analyzers downstream to ensure adequate phosphorus removal.
In the simplest implementation of the control system the IQ SensorNet system sends a proportional 4 to 20 mA signal to the customer’s SCADA system, or directly to the feed pump, to control chemical based on feedback from the orthoP analyzer. A feed forward control system calculates the required chemical feed rate based on upstream orthophosphate concentration and measured wastewater flow. The IQ SensorNet can easily be programmed by the customer, providing the flexibility to tailor the chemical dosing to the demands of the specific plant design and wastewater characteristics.
At the Watertown WWTP, orthophosphate measurements from a P700 IQ are taken every 15 minutes and fed into software that was custom-developed for Watertown by Starnet Technologies. Using records dating back to 2003, -when the Watertown facility was commissioned, Freber and the software team correlated historic orthophosphate, ferric chloride and final total phosphorus levels to build an algorithm to govern chemical inputs.
The system reacts to readings from the P700 analyzer by adjusting pump speeds in 5 Hz increments across a range from 5 to 60 Hz. The screenshot in Figure 2 illustrates how the system works. The pump speed, in green, is maintained at a minimum level until the orthophosphate (OP) concentration, in blue, rises above the programmed 0.7 mg P/L setpoint. Pump speed increases until the OP concentration peaks and starts to decrease. Pump speed returns to minimum speed again when the OP concentration falls below the setpoint.
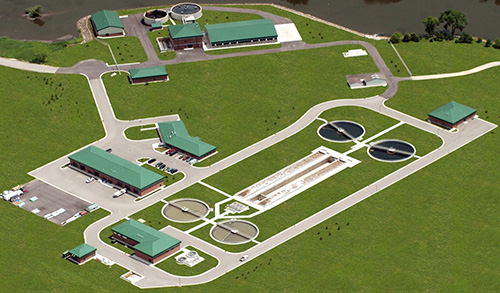
Aerial view of the Watertown WWTP
“Once we got the program set up so the actual orthophosphate readings meant something to run the ferric chloride pumps, it was easy,” says Freber. “It just walks itself up and ramps itself down. It’s just ‘set it and forget it,’ and we’ve got the comfort of knowing we won’t be exceeding our 1 mg TP / L limit.”
Great Fit
Freber says his experience with manufacturers’ rep Mulcahy Shaw and YSI made the move to automation—and the upgrade to the new P700 IQ—smooth and easy.
“Mulcahy Shaw are a great bunch of people to work with,” he says. “Tom Mulcahy really cares about his customers, and he worked hard to get me the new unit. They shipped the P700 to us, my mechanic hooked it up, and Mark Duerr from Mulcahy Shaw did a one-and-a-half-hour training. That’s all it took.”

The City of Watertown Wastewater Treatment Plant Settling Tanks
“The reps work really hard, and I know YSI works really hard to put out a quality product that’s really going to help the customer,” he adds.
The IQ SensorNet P700 IQ helped the Watertown team in more ways than one. Their community of 24,000 residents prides itself on its state-of-the-art, eco-conscious wastewater treatment facility, whose dewatered biosolids “cake” is applied on farms nearby.
“The investment in automating phosphorus management paid for itself quickly,” says Freber.
“This is huge, and not just for my budget. I sold the concept because we’re using so much less chemical.”
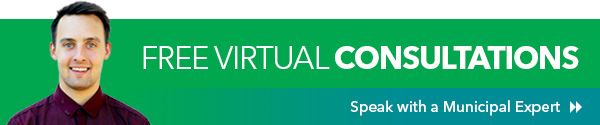
Additional Blog Posts of Interest
Operational Efficiency with SCADA and Continuous Process Monitoring
Activated Sludge | Three Steps to Improve Your Process Efficiency
The Science of Phosphorus | Blog Series | 1 of 5
Monitoring Orthophosphate for Reduced Chemical Costs in Water Resource Recovery Facilities