Wastewater Aeration Control Cost-Benefit
It has been estimated that dissolved oxygen control systems in water resource recovery facilities reduce energy consumption compared to manual control by 50 to 100 kWh per million gallons treated1. Implementation of DO control at the Sheboygan, Wisconsin wastewater treatment plant reduced energy consumption by an estimated 459,000 kWh, approximately 105 kWh per million gallons treated2.
The estimated cost savings was $65,000 annually resulting in a simple payback of fewer than two years. Interestingly, the DO control component was not part of the original project which included new blowers. It was only added after operators were unable to control wide fluctuations in DO. The new control system more than doubled the energy savings for a much smaller investment. 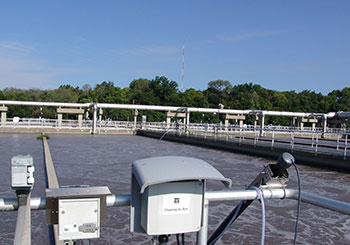
The J.D. Phillips Water Reclamation Facility in Colorado Springs, CO implemented ammonium-based aeration control to minimize aeration energy for nitrification. A brief trial period demonstrated that an estimated annual energy savings of $50,000 could be achieved by simply reducing the DO setpoint during daily low flow periods3.
The above examples aside, evaluation of cost-benefit for aeration control projects is not straightforward.
Energy savings as a result of a control project are not typically reported if the accounting is even performed. One important reason is that assigning costs and benefits is challenging. Wastewater treatment plants are complex and so are the improvement projects that include control components. Multiple improvements are usually bundled together, for example switching to another form of aeration or replacing diffusers or blowers. It is no easier to assign benefits. Utilities do not keep track of expenses at the process or system level.
For example, electric submetering of equipment is not typical. Nevertheless, it makes sense that aeration control saves energy and reduces operating costs. The strong and growing interest in aeration control projects is evidence that utilities see the value in aeration control. Simple examples shown below demonstrate energy and cost savings potential.
Energy Cost Savings Example Calculations
A hypothetical example demonstrates the potential energy savings for various aeration control strategies based on the following assumptions:
$ = hp x 0.746 x $/kWh x (# hours/day)
hp is total horsepower and 0.746 is the conversion from hp to kW.
Blower hp: 200 hp
Mechanical Mixer hp: 40 hp
Energy cost: 10.42 cents per kWh (Source www.eia.doe.gov – average for April 2021)
Affinity laws for centrifugal blowers dictate that the blower air flow varies in direct proportion to the blower speed and that power varies with the cube of the blower speed:
CFM2/CFM1 = RPM2/RPM1
HP2/HP1 = (RPM2/RPM1)3
Constant Airflow Mode – No Control
Electricity costs to run a blower full speed for 24 hours per day for a 1 MG aeration basin:
(200 hp) x 0.746 x $0.1042/kWh x 24 = $373 per day
$373 per day x 30 days = $11,190 per month - no savings
Discussion: Aeration blower is run full speed around the clock regardless of the oxygen demand. The strategy is to provide enough air to maintain a minimum DO concentration at the highest loading condition. At lower loading conditions, especially overnight, aeration would be far in excess of what is needed. Energy and money is wasted.
On-Off Aeration with Timers
Electricity costs savings for a blower that is shut off once per hour for 15 minutes would be:
(blower hp – mixer hp) x 0.746 x $/kWh x (# minutes / hour) x 24 = $ per day
(200 hp – 40 hp) x 0.746 x $0.1042/kWh x (15/60 x 24) = $~75 per day
$~75 per day x 30 days = $~2,250 per month saved
Discussion: Blower is operated intermittently on a timer reducing energy consumption. At peak diurnal loading condition, the system may fail to maintain an adequate DO concentration reducing the quality of treated effluent. At minimum loading, e.g. overnight, aeration may exceed treatment requirements causing the DO concentration to spike. This strategy could possibly be tuned for shorter air off periods at peak loadings or longer air off periods at minimum loadings depending on the SCADA. However, without feedback, the system is not optimized. The tendency would be to set intervals conservatively to meet the worst anticipated loading condition and adjust infrequently. The calculation takes into account the energy for mechanical mixing which would be required during blower off periods to keep mixed liquor in suspension but not additional capital cost for mixers.
On-Off Aeration with Feedback
Electricity costs savings for a blower that operates continuously 4 hours per day, shuts off 15 minutes per hour for 12 hours per day, and shuts off 30 minutes per hour 8 hours per day would be:
(blower hp – mixer hp) x 0.746 x $/kWh x (# minutes / hour) x # hours = $ per day
(200 hp - 40hp) x 0.746 x $0.1042/kWh x [(15/60 x 12) + (30/60 x 8)] = $124 per day
$124 per day x 30 days = $3,720 per month saved
Discussion: The energy savings compared to sequencing control with timers is not substantial in this example. However, feedback control would provide assurance that treatment requirements are met no matter what the loading condition enabling the highest energy conservation possible with on-off control. Mechanical mixing is required as with sequencing control.
PID Aeration Control with Centrifugal Blowers
Electricity costs savings for a blower that runs at full speed 4 hours per day, 75% speed 12 hours per day, and 50% speed 8 hours per day would be:
(200 hp) x 0.746 x $0.1042/kWh x {[1 - (0.75)3] x 12 + [1 – (0.50)3] x 8} = $171 per day
$171 per day x 30 days = $5,130 per month saved
Discussion: PID control easily offers the greatest potential energy savings. However, there will be a one-time cost for a project to purchase, install, and program the controls equipment required. Case studies have demonstrated that the simple payback for installing DO control equipment is a few months to a few years (USEPA, 2010). The high cost of blowers means that payback periods are much longer if blowers must be upgraded in order to meet the design points.
Summary
Summary of Calculations Strategy
|
Energy Cost Per Month |
Energy Cost Savings Per Month |
No control |
$11,190 |
- |
Sequencing with timers |
$8,490 |
$2,700 |
Feedback on/off control |
$8,040 |
$3,150 |
Feedback PID control |
$3,390 |
$7,800 |
1 Burton, F. (1998). Saving on Wastewater Treatment. Energy Magazine, 17-20.2 Environmental Protection Agency (USEPA). (2010). Evaluation of Energy Conservation Measures for Wastewater Treatment Facilities.Washington, D.C.: USEPA.3 Brischke, K. K. (2010). Using Whey as a Supplemental Carbon Source under Real Time Control Conditions. WEFTEC Proceedings. WEF.
Additional Blog Posts of Interest:
What's Next for Water Quality Sensor Trends in Wastewater?
Myths and Realities: Ammonium Based Aeration Control in Wastewater
Troubleshooting Nitrification and Denitrification in Wastewater
Shortcut the Nitrogen Removal Process in Wastewater with UV Sensors