Water Quality Sensor Trends in Wastewater
Smart devices have transformed nearly every aspect of our home and work life: smartphones, smart televisions, smart appliances, even smart homes. Process instrumentation for wastewater monitoring and control is no exception. The online sensors available today are far superior to versions available just 10 years ago providing more measurements more reliably, and at a reduced cost. 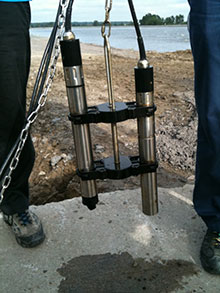
As a result, there are more opportunities for enhancing the performance and efficiency of water resource recovery facilities (WRRF). YSI’s solution for online process monitoring, IQ SensorNet, is a network-based, modular system. Each of the four basic components of the system
- sensors
- cables
- modules
- controllers
has features that make implementation simple and effective. This post will focus on the sensor component of the system.
Smart Sensors
The most evident part of any measuring system is, of course, the measurement. The IQ SensorNet features smart sensors for measuring the 20 most critical parameters for the operation of WRRFs.
The basic sensor configuration is a 40 or 60 mm probe that is immersed directly in the process water and makes measurements without the need for sample transport and processing or input of external reagents. Internally, each sensor consists of the same analog sensing elements as ‘dumb’ sensors, electrodes for example.
In addition, solid-state electronics built into a smart sensor evaluate continuous analog signals internally and process the signals into a measurement value. This configuration makes it possible to process multiple signals such that the number of measurements is limited only by the number of analog sensing elements that will ‘fit’ on the probe.
The measurement values, say mg/L ammonium and nitrate, are transmitted to a universal controller in the form of discrete (digital) values. In contrast, ‘dumb’ sensors also require a separate unique instrument (transmitter) for each measurement type. This feature greatly simplifies the operation and flexibility of the system. For example, calibration data are stored in the sensor. As a result, sensors calibrated at the factory may never require calibration by the end-user. Calibration of other sensors is much more convenient. For example, YSI VARiON ammonium and nitrate sensors require only a single-point matrix adjustment which is performed without having to remove the sensor from the process. Another example, YSI SensoLyt online pH and ORP sensors can be removed from the process, detached from the cable, and calibrated in the lab or other convenient location.
In addition to the measurement, smart sensors also transmit identification and status information electronically. A sensor connected to the IQ SensorNet is recognized automatically and the measured value is displayed immediately (plug and play). Status information helps the Operator quickly identify a problem and the proper solution.
For example, when the sensor cap on the optical DO sensor (FDO) becomes depleted and needs replaced or the suspended solids sensor (ViSolid) becomes fouled. Furthermore, each sensor has a common built-in digital communication interface. As a result, multiple sensors of various types can be conveniently connected to universal controller. A single IQ SensorNet network allows a combination of up to 20 different parameters, over two times more sensors than any comparable system on the market, substantially reducing hardware requirements.
Acquisition Cost
The acquisition cost for smart sensors is higher but not by a large margin and the difference is getting smaller all the time. The cost difference per measurement shrinks and even reverses, the more measurements required taking into consideration the cost for multiple transmitters and installation. Regardless, the substantially greater functionality makes it worth any marginally higher cost for most customers. For this reason, smart sensor technology is fast becoming the standard.
YSI IQ SensorNet sensors are designed for the best possible accuracy in WRRF environments and the highest repeatability. The angled sensor cap of the FDO optical dissolved oxygen effectively sheds air bubbles from diffused air systems providing an accurate and stable measurement down to concentrations less than 0.5 mg/L.
The first figure below compares the measurement between an FDO sensor and a competitor’s sensor with a flat sensor cap in the typical “nose down” installation. The sensor with the flat cap exhibits higher, more erratic readings.
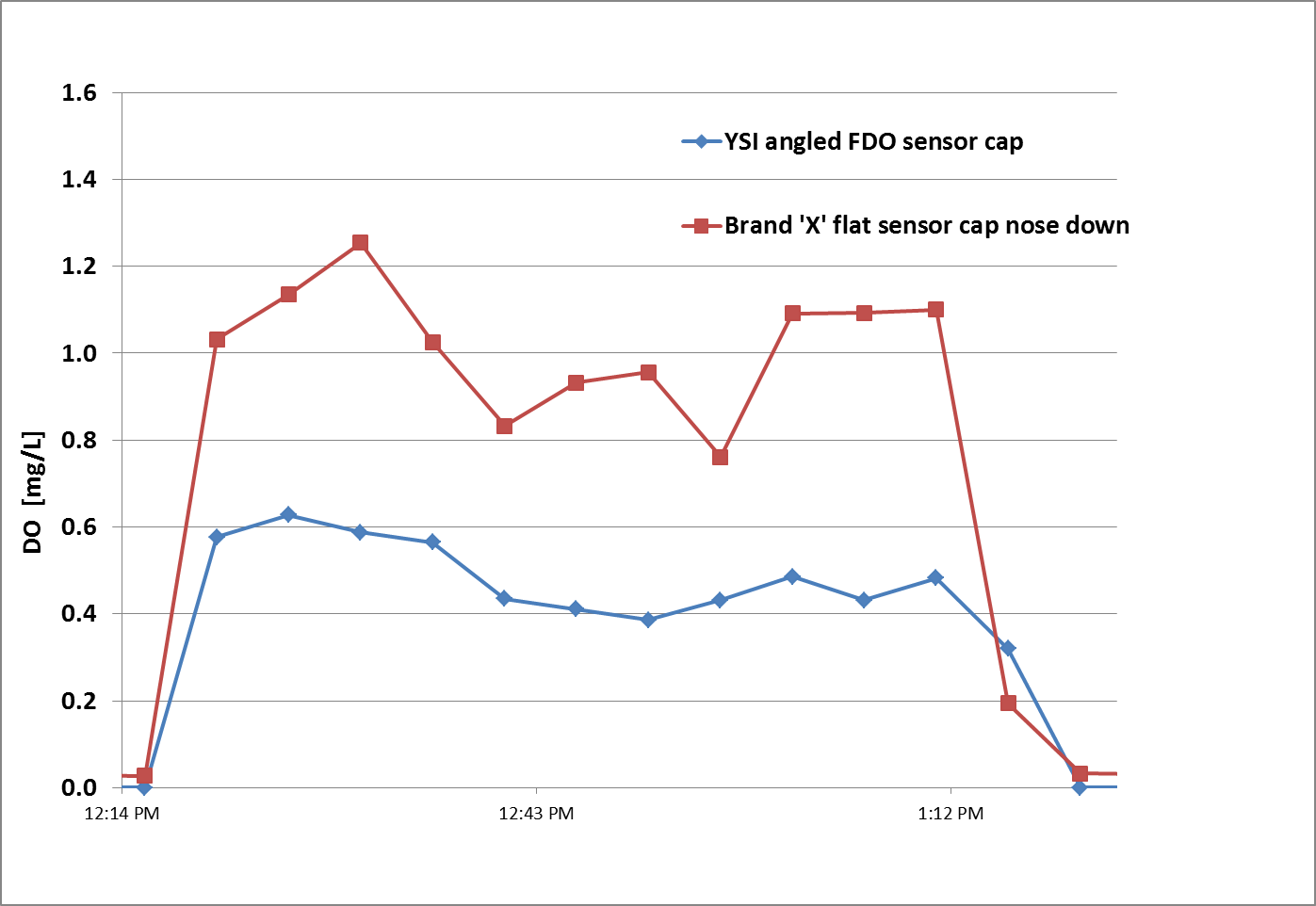
The second figure compares the data from the sensors in an inverted condition. The Brand ‘X’ sensor reading is less erratic and in closer agreement with the FDO sensor demonstrating the higher accuracy of the FDO due to the reduced effect of air bubbles.
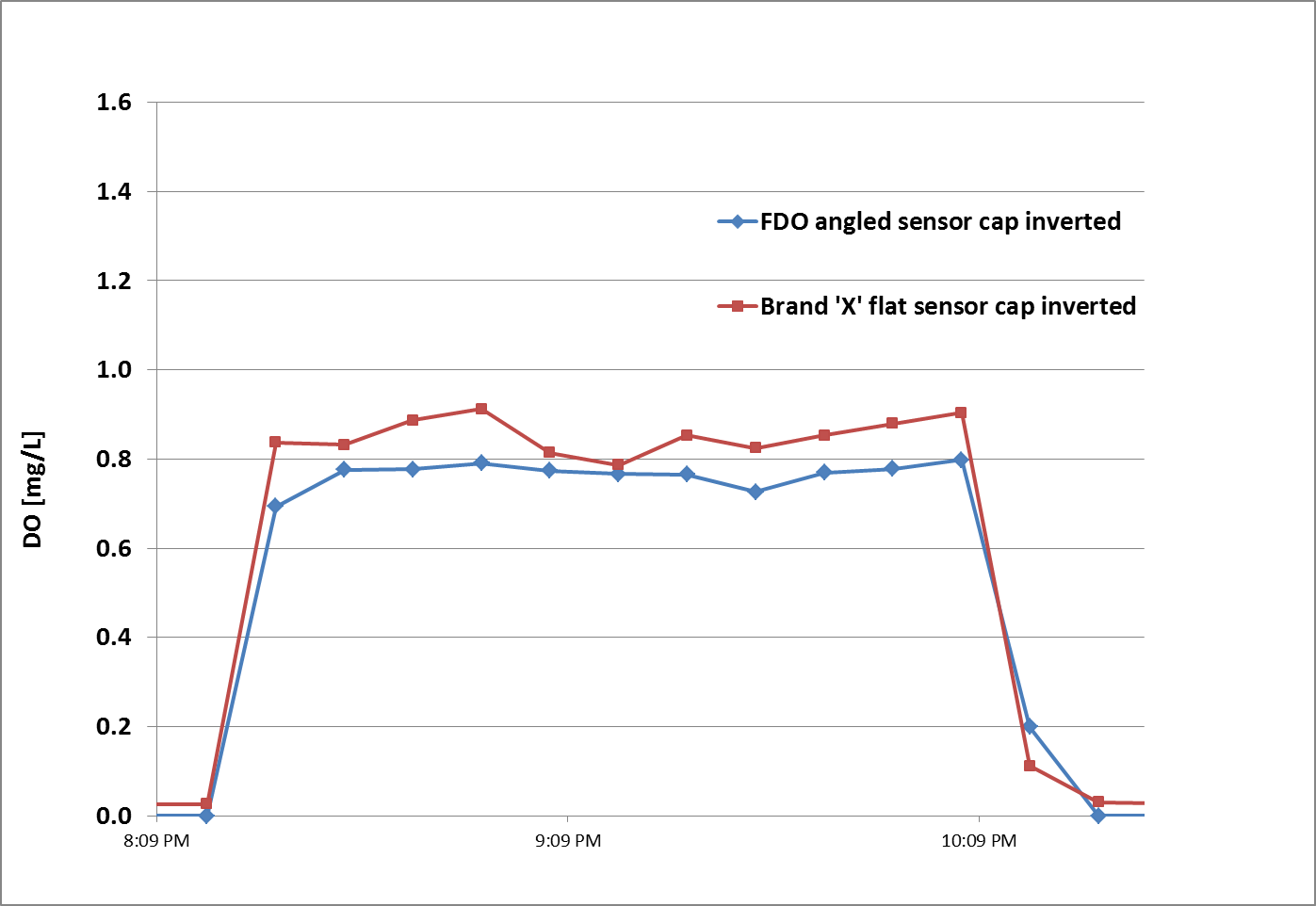
Additional Blog Posts of Interest:
Biological Nutrient Removal Applications for Monitoring ORP
Can Smart Devices Enhance Water Resource Recovery Facilities?
Shortcut the Nitrogen Removal Process with UV Sensors
Ion Selective Electrode (ISE) Measurement - Fundamentals in Online Analysis