Super Intensive Aquaculture of Shrimp
Producing more than nine kilograms of Pacific White Shrimp per cubic meter, a research team led by Dr. Tzachi Samocha at Texas AgriLife Mariculture Research Laboratory in Corpus Christi, Texas is forging a path that is allowing producers to thrive in spite of the razor-thin margins of the shrimp market. 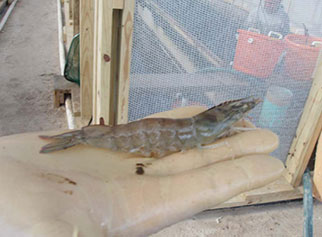
The team’s super-intensive shrimp production system relies on precise management, high biomass, and biosecurity to stimulate outstanding growth and drive production costs down from above $5.00 per pound – the U.S. average for superintensive systems in 2009 – to approximately $2.00 per pound. The three-month grow-out period allows nearly four crops per tank per year. Coupling those production efficiencies with sales to high-value fresh or never-frozen regional markets is making shrimp profitable to many growers again, says Samocha.
Samocha’s indoor, limited-discharge, super-intensive system is stocked at 530 shrimp per cubic meter, a radical departure from the conventional outdoor ponds raising 100 to 150 shrimp per cubic meter. But high-intensity production demands high-intensity management, especially because the system’s dissolved oxygen (DO) levels are marginal at best – and they drop precipitously at feeding time.
“We’re always on the borderline, pushing the envelope on DO,” says an aquaculture technician in Samocha’s lab. “When we add feed, you can literally watch the DO drop. In 30 minutes, you’ll see it go from 4.5 milligrams per liter (mg/l) to 3.5, or from 4.0 to 3.0. You ride the balance between life and death.”
Those rapid declines and the slow DO recovery to safer levels after feeding, demand careful scrutiny. It is also vital to maintain a constant track of DO levels to determine whether pumped air will be adequate to restore DO, or whether more costly liquid oxygen is necessary. In the super-intensive system, every liter of oxygen can affect survivability – and profitability.
Limited-Discharge Raceways
Though they are called raceways, the four greenhouse-enclosed, 40-cubic-meter tanks in Samocha’s trial are not raceways in the classic sense, as there is no inlet or outlet. Water is retained in the system to avoid introducing pathogens through intake water and incurring environmental costs at the discharge. Municipal water is added to replace water lost to evaporation, approximately one percent of the total volume per day. 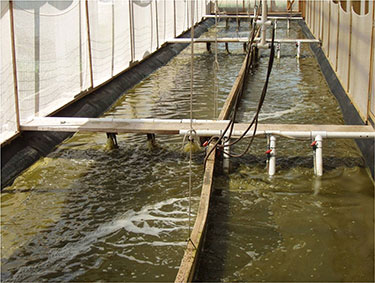
Managing oxygen is the cornerstone of the operation. Each raceway is equipped with a series of eighteen 5.1-cm airlift pumps, six one-meter-long air diffusers, and a partition running down the centerline to keep water circulating in the proper direction. Under the partition, a 5.1-cm PVC pipe is positioned to deliver air from a Venturi injector powered by a 2-hp pump.
Remarkably, Samocha and his team supplied the system’s oxygen needs with atmospheric air and the Venturi injectors until biomass reached approximately 7 kg/m3 on Day 73. On Day 74, the team began enriching atmospheric air with liquid oxygen at an average of 3.5 liters per minute (lpm) for the remaining 20 days of the study.
The raceways are heavily colonized with bacterial flocs and microalgae in the limited discharge environment. The bacteria contribute to high solids in the water – the team’s target for total suspended solids (TSS) was 500 mg/l.
“The benefits you get from the bacterial flocs are stability of water quality and contribution to shrimp nutrition,” says Samocha. The bacteria assimilate nitrogen compounds that can be harmful to shrimp, he explains. Furthermore, initial indications suggest that these bacteria may also be used as a source of feed or biofuel, he notes.
Unlike algae, the bacteria constantly consume oxygen rather than produce it. These bacteria do not create major daily shifts in DO. “With bacterial flocs, you don’t see the huge diurnal flux that you see in outdoor production systems,” the technician explains. “The shrimp like that. They can deal with these DO levels of 4.0 as long as they’re constant. In an algae-based, green-water system, DOs are typically nice and high during the day, when the sun is out. But at 4:00 every morning, they can go down to 2.0. When it does that day after day, it’s stressful for the shrimp.”
Constant Monitoring
The team analyzes water samples weekly for alkalinity, settleable solids, turbidity, algal counts, total suspended solids (TSS), volatile suspended solids (VSS), carbonaceous biological oxygen demand (cBOD), ammonia, nitrite and nitrate-nitrogen, and reactive phosphorus.
But oxygen management can’t wait a week. During the early stages of production, DO and pH are monitored at least twice daily with handheld instruments such as the YSI Pro1020. As the shrimp grow, water quality decreases and oxygen demand increases. At around 30 days into the production cycle, Samocha’s team deploys YSI 5200A continuous monitors, which they set to log DO and temperature readings at five-minute intervals and trigger an urgent alarm on their computer monitors if levels drop below chosen thresholds. 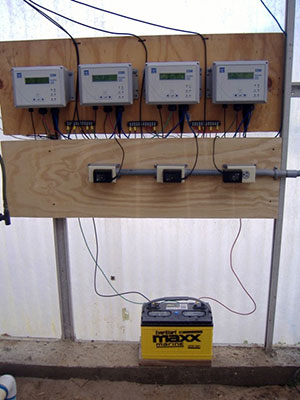
“It’s very crucial that you stay on top of things and modify your management accordingly,” cautions Samocha. “If oxygen is low and you are dumping in feed, I can guarantee within a few minutes you will have stressed shrimp at the surface. If you don’t have this monitoring system, it is very risky for your production.”
The probes of the continuous YSI monitor are positioned in front of airlifts to ensure a steady flow of water over the sensors, reducing biofouling. In the nutrient-rich water, wiping the probes occasionally is still important to keep them clear of biofilm.
YSI 5200A – which can simultaneously monitor temperature, DO, pH, conductivity, oxidation-reduction potential (ORP) and salinity – is designed specifically for the punishing conditions of aquaculture. In addition to continuous monitoring and alarms through audio signals, emails, and even phone alerts via a hookup with a Sensaphone® remote monitoring system, the 5200A can also be programmed to control pumps, paddles, liquid oxygen valves, and feed systems.
Samocha’s team uses YSI AquaManager software to record and display the data from the 5200As. The system allows them to not only monitor the system in real time at the lab and remotely from a home computer, but also to track trends over hours and days. That’s vital, especially because the super-intensive production tanks periodically experience slow downward trends in DO.
“The monitoring system allows us to act before something happens, rather than react to an emergency situation. It takes a lot of the guesswork out. We can start planning ahead.” 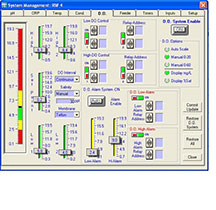
Super-intensive shrimp systems have a great potential to go commercial, producers will continue to take even more guesswork out of the equation by utilizing the automation capabilities of instrumentation like the 5200/5200A (or 5500D optical DO monitor), including managing DO and temperature as well as conditional feed timing, which factors in biomass, feed conversion ratio and environmental conditions when electronically engaging feeders.
Fine Detail
In fact, one of the most significant adjustments that have arisen from continuous, real-time monitoring of the system is the fine-tuning of the feed regimen.
Until Day 56 in the study, the shrimp were fed four times daily, at 8:30 and 11:30 am and 2:30 and 4:30 pm. When biomass reaches 6 kg/m3 and DO drops too precipitously after feeding, the four daytime feedings were cut back to one to two-thirds of the total ration, with the remainder metered out at night with belt feeders.
In the end, Samocha’s system yielded an impressive average feed conversion ratio as low as 1:1.2 and a weekly gain of 1.3 g/week to produce as much as 9.23 kg of marketable-sized shrimp per cubic meter. The closed system successfully prevented viral outbreaks, and mortality was held below 0.5 percent per week.
Samocha and his team penciled out the economics of a year-round, commercial installation of the super-intensive, limited discharge system. Assuming the operation built eight 500 m3 grow-out tanks and two nursery tanks to produce an average of 3.8 crops per year would cost USD $992,000, they figured. At a price of $3.27 per pound for 21-to-25-count shrimp and production costs of around $2.60, the system could pay itself off in about 3.1 years and deliver an internal rate of return of more than 28 percent. And without the regulatory challenges and the cost of discharging and replacing water, the system has extra appeal in the tightly regulated U.S. market.
That paints a bright future for super-intensive shrimp production. And with skilled operators and reliable, continuous monitoring and control, it gets brighter and brighter.
Additional Blog Posts of Interest
Nitrate Levels in Aquaculture May Be More Dangerous Than You Think
Improving Efficiency with Aquaculture Monitoring and Technology
Aquaculture Raceway Shrimp Production with Dissolved Oxygen Monitoring