Efficiency is the key to success in shrimp production—creating the conditions for shrimp to efficiently convert nutrients into body weight, and running a business that achieves that conversion efficiently. The NaturalShrimp Company, on the outskirts of San Antonio, Texas, has turned efficiency into an art form, supplying an eager market with weekly harvests of fresh, chilled shrimp. 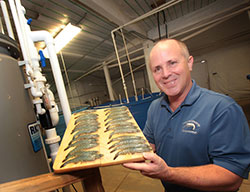
Since its inception, the company has mastered the art of recreating the ocean environment in a recirculating, biosecure inland environment, ideal for environmentally friendly, high-density production of Pacific white shrimp (Litopenaeus vannamei).
NaturalShrimp’s proprietary system maintains water quality in its tanks. But it’s not easy.
“These systems are not rocket science,” Doug Ernst said. “They’re harder than rocket science. Rocket science is predictable, not chaotic. Any time you’re working with a biological system, there’s an element of chaos and unpredictability. Even in controlled systems, there’s some element of chaos.”
The Gas Pedal
With various water treatment technologies used to manage shrimp metabolites such as ammonia and long-term accumulation of nitrate, the other critical challenge is maintaining a healthy growth rate in the tanks. Temperature and oxygen are the fundamental parameters, said Ernst, and have been managed automatically since NaturalShrimp installed its first YSI 5200 multiparameter continuous monitoring systems at start-up.
But the true driver of the production system is NaturalShrimp’s automated feeding system, which is managed by YSI’s Feed SmartTM feed timer system, a fully automated program designed for YSI’s aquaculture monitoring products (5200A, 5500D, and 5400).
“Basically, what it all comes down to is that feeding is like the gas pedal of the engine,” said Ernst. “The definitive thing in all aspects of aquaculture is how much feed you’re putting into the system, at what rate. That drives your oxygen demand. It drives your metabolic loading.”
NaturalShrimp starts with PL10 hatchery shrimp and grows them out to harvest size. Based on population, weekly body weight samples, and feed conversion ratio for L. vannamei, they program the YSI monitors to deliver precisely enough feed each day to meet growth targets.
“Feeding rate is a function of species, mean body weight and temperature,” Ernst noted. “We set the panels once a week and they grow that crop each day, going up each day a little bit. The logic of the panel is very much in-sync with the logic of our feeding.”
Steady as She Goes
One of the highlights of the YSI Feed Smart feed timer system is the ability to steadily deliver feed over a 24-hour period—a pattern that is critical to dealing with shrimp, Ernst points out.
“Shrimp are different from tilapia or salmon in that they have a very short gut,” he explains. “They don’t really have a stomach they can fill up—they’re not event feeders. They’re continuous grazers.
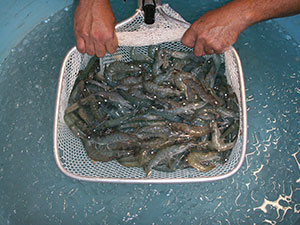
“If you have an animal that will basically eat 24/7, the best way to administer that gas pedal is to keep it steady and even,” Ernst says. “That spreads out the loading in the system.
Therefore it spreads out the oxygen demand and spreads out the excretion of ammonia and carbon dioxide. There’s less load in the system, and it makes the system more stable and robust.”
Less Waste
Because the YSI system only provides as much feed as will be eaten in the specified feeding interval—programmed into the control panel as the number of feeding events per day—waste is reduced dramatically.
“When the pelletized feed hits the water, it will start to leach nutrients, start softening, start being digested by microbes in the water, and lose nutritional value over time,” Ernst explains. “You want to put your feed in and have it eaten, basically the quicker the better. The higher the feeding frequency, the more feedings per day, the better the nutritional delivery to the shrimp.”
For aquaculture systems in general—both biofloc and filtration-based technologies—uneaten feed goes straight to the bottom of the microbial food chain, the bottom of the tank, or the bottom of the waste solids removal…and therefore to the bottom line.
Reduced Labor Costs
“The other big concept in automated feeding is the reduction of labor,” Ernst points out.
“In a full facility, if you’re manually feeding all the time, then you’re talking about swing shift and graveyard shift, and somebody coming in on the weekend. Just to get that feed out, you’re talking about 24/7 staffing. It would work out to an extra 4.2 full-time equivalent (FTE).
“With those costs, you might not feed continuously—you’d divide that and your waste feed would go up.”
The YSI 5200A system replaces that labor with a simple desktop interface that is easy to program for up to 100 feedings per day, measured in ounces and pounds or grams and kilograms. The system increases feed daily based on user-defined feed conversion ratio (FCR), either in Continuous or Timed modes.
The YSI 5200A can also decrease feed levels based on dissolved oxygen (DO), temperature or pH values, defined by the user—in Ernst’s metaphor, applying the brakes to metabolism until the system is stabilized.
NaturalShrimp has consistently used the Feed Smart system to its best advantage, notes Darrin Honious of YSI in Yellow Springs, Ohio. “Doug and his staff have a phenomenal understanding of the nutritional needs of their shrimp, and use the Feed Smart feature as part of a finely honed system,” Honious says. “The results speak for themselves, in the extraordinary quality of their shrimp and their consistent improvements in efficiency across the operation.”
Temperature Control
Ernst uses his YSI monitors to keep constant track of temperature and DO, though the YSI 5200A is also capable of monitoring conductivity (salinity), pH and oxygen reduction potential (ORP). Ernst also manually samples for ammonia.
“Really, temperature, oxygen, and feeding are the core management variables of the aquaculture environment,” Ernst says. “We use the panels to manage our in-tank heaters. The panel can turn on and off the heat so our water temperature is always at the appropriate temperature. And if oxygen goes below a certain point, it can turn on pure oxygen. If oxygen falls farther than that, the YSI panel will call the autodialer.”
Ernst says NaturalShrimp’s YSI controllers have grown with the company’s business.
“As we’ve seen improved growth rates over the years, we can input that into the panels,” he notes.
That flexibility has led to a tremendous trust in the automated feeding system.
“It’s been an unchanged part of our technology for eight years,” Ernst notes. “It’s reliable, it’s functional and it’s programmable. It’s an agent out doing our bidding. We just load the hoppers in the morning and off we go.”

Additional Blog Posts of Interest:
Improve Efficiency with Aquaculture Monitoring & Control Technology
YSI Appily Introduces this Appsolutely Great Apportunity - Aquaculture App
Aquaculture Raceway Shrimp Production with Dissolved Oxygen Monitoring
Nitrate Levels in Aquaculture May be More Dangerous than You Think