Sustainable Aquaculture Seafood Production
(Updated November 2021)
With an increasing demand for sustainable seafood production, there is a growing trend for land-locked farmers who once raised hogs or cattle to turn to fish farming indoors. When Leland Meador’s family left the hog farming business, he knew he wanted to convert the unused swine barn into an indoor aquaculture facility. 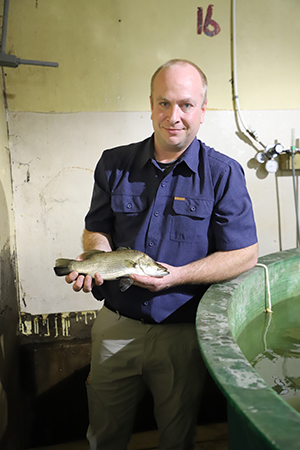
Leland, Owner/Operator at Hanilu Farms, had experience working in aquaculture and knew that there was a high demand for sustainably-raised seafood. Aquaculture is projected to be the prime source of seafood by 2030 due to growing consumer demand and depletion of the ocean’s resources. (Learn more, Aquaculture blog posts).
In 2017, the barn was converted into a closed containment Recirculating Aquaculture System (RAS), in which aquatic organisms are raised in reused treated water. The RAS, which is located in central Indiana and is currently beyond its first year of operation, is a 34-tank, 112,000-gallon facility that produces around 2,000 pounds of fish per week year-round. These systems allow for high-density production in small spaces and are considered one of the most environmentally sustainable aquaculture methods. RAS facilities conserve water and minmize effluent production (waste), reducing the environmental impact of the operation.
The farm raises Australian barramundi, also known as Asian sea bass, for sale on the live fish market. At one inch and weighing about 1/4 gram, the barramundi fingerlings are shipped from Australia directly to Leland’s facility, raised in the RAS until they reach approximately 1.5 pounds, and are then sold. Because the health of the fish is crucial, each tank needs to be closely monitored to keep an eye on dissolved oxygen (DO) and temperature levels. Dissolved oxygen control is critical in aquaculture. Barramundi will typically grow and thrive within a DO range of 5-12 mg/L (ppm). If levels drop below that, the fish may become stressed, stop feeding, and begin to die off.
As far as losing fish to an oxygen crisis, I have not lost a single fish with the YSI oxygen monitoring system. It has never failed.
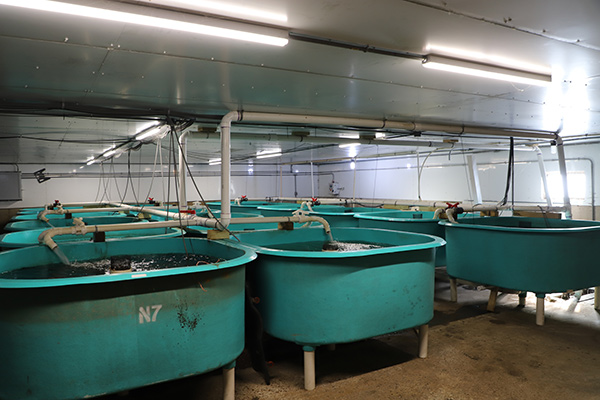
Barramundi fingerlings are raised in smaller tanks (above) and once they are big enough, they are moved to grow-out tanks in another part of the facility.
A common method of monitoring DO and temperature levels are by spot-checking with a handheld instrument. Hanilu Farms uses a YSI handheld DO meter to collect and log data manually. The handheld is reliable, provides accurate data, and uses an optical-based sensor to measure DO. The instrument works well for quick spot-checks, but the farm was looking for a way to monitor dissolved oxygen and temperature levels continuously without a staff member onsite.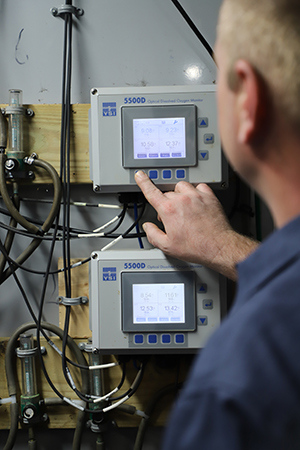
YSI provided an effective solution with 5500D continuous water quality monitors and the Aquaviewer II app, which displays data and sends alarm notifications to your mobile phone. (Learn more, How Aquaculture Facilities Benefit from Automation).
The farm installed five YSI 5500D monitors in three locations throughout the facility to accurately monitor water quality. Each monitor has 4 probes, and each probe has an optical DO and temperature sensor.
All of the measurements logged by the instruments are displayed in the Aquaviewer II app in real-time, making the data available anywhere, anytime. Alarm notifications are sent via badge notification, text and email so staff can keep a close watch on the water quality conditions.
The monitoring system is easily expandable, with the ability to add new monitors and probes at any time.
We are in our second year of operation and I’m happy to say that YSI monitors have yet to fail in letting me know when the oxygen is low.
The farm has been using the YSI monitors for 2 years and Leland is pleased with the results and the time saved. The farm hasn’t lost a single fish due to low oxygen since the monitors were installed. Leland contributes that to the accuracy of the 5500D data, saying “I’ve checked and rechecked the oxygen levels with my handheld ODO multiple times, and every time I check, the monitors are always within their calibrated points.”
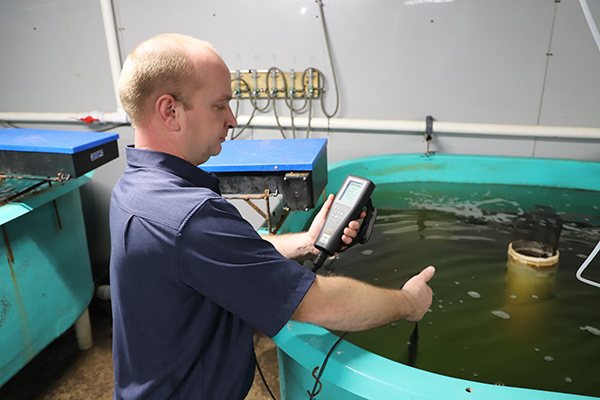
Leland uses YSI handhelds to spot check DO and temperature in one of the facility tanks.
With operations running smoothly, Leland has future plans to increase production due to high demand. To save even more time, he plans to utilize the automation capability of the 5500D, which uses relays to control heaters, automatic feeders, and solenoid valves for oxygen delivery. The farm will automate oxygen with a pre-defined alarm that triggers a valve to open if oxygen levels drop too low, allowing more oxygen into the tank without the requirement of sending someone onsite.
“I chose YSI because it was easy. It’s one of the only systems that is made for an actual aquaculture facility” says Leland. “If I didn’t have the YSI system, I probably wouldn’t be in business today.”
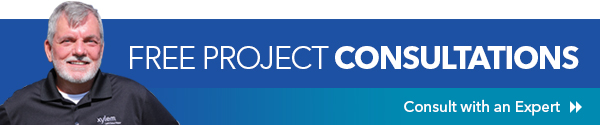
Additional Blog Posts of Interest
Sustainable Aquaponics Farm Reduces Crop Failure
How Aquaculture Facilities Benefit from Automation
Sustainable Land-Based Atlantic Salmon Production