Interested in a Monitoring Buoy? You Need to Know These 5 Things
(Updated November 2021)
Maybe you’re an expert in hydrology or harmful algal blooms, but you don’t know the first thing about selecting a buoy for environmental monitoring other than it floats and is sometimes tricky to spell. (I always think “bouy” looks right. Its’ not.)
Maybe you’ve recently decided that routinely taking a boat out to collect water quality data is taking too much time or is too tricky with unpredictable weather or workloads. Maybe it’s not safe.
Perhaps you just want more data.
In other words, maybe it’s time to look into a water monitoring buoy, but you haven’t quite gotten there because you get bogged down in online descriptions of things like buoyancy and sea state, and “tackle” is a term you’ve only used when you talk about fishing.
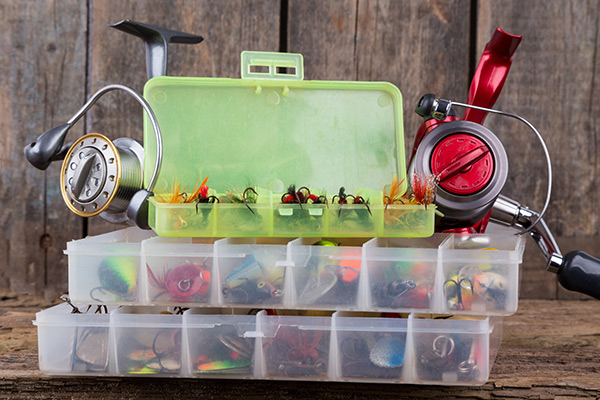
This all describes me recently, as I’ve taken on the task of managing a line of integrated system products that include buoys. With help from YSI’s buoy experts, what I’ve realized is that I don’t need to be a buoy expert (relief!), as long as I approach an expert ready to discuss five key things: the monitoring environment, sensor payload, logging & telemetry, power, and deployability.
We recently developed an online tool that can help you quickly get to a possible buoy solution, and you will see that these five things are built into the logic behind that easy-to use tool. The questions might not get you to the perfect solution, but they’ll jog your thinking and get you ready for a conversation. If you prepare yourself to discuss these things with a YSI specialist, we can customize the best buoy to fit your application and your budget!

1: What's the Environment?
Depth, flow, wind and waves are the environmental characteristics you need to consider at a minimum when you come to the table to discuss buoys.
Come ready to talk about depth at the monitoring position and the path to get it there in terms of 5-10 m ranges. In one respect the importance of depth is obvious: if your pond is 3 ft deep and you’ve got a 3 ft stainless steel tube for a sonde on the bottom of the buoy, that’s not going to work. Less obvious is that the depth that the buoy might have to traverse before you place it needs to be evaluated. How will you get it to its final position? Will you be unloading it at a boat ramp? Towing it from a littoral zone that might have a steep slope or rocky bottom? Of course some buoys are just too big for shallow waters, but a buoy can also be too small for really deep waters, even if those waters are calm. The buoy will need to bear the weight of tackle to anchor, and the deeper the site the more mooring tackle may be needed.
Flow, wind and waves all exert forces that will affect not only the size but also the construction and moorings. For example, most standard buoys are poorly suited for rivers and inlets because of flow, especially if flooding or flow path changes are risks. Rather than a round buoy that most of us think about, a catamaran design like YSI’s Pisces may be a better option for rivers. This was the case for a project in Thailand, where the Pisces was the best choice for a government monitoring program that included the Pa Sak River.
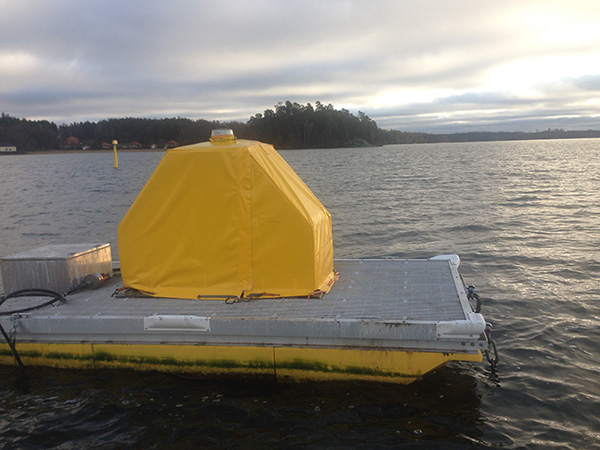
Waves can be described by height, and winds in miles (or km) per hour. Waves and wind are often used to collectively describe the sea state, which is a scale from 0 to 9 describing the calmest to the most treacherous conditions. Truly knowing the sea state of your site is tricky if you’re new to the concept, and you might not have all the information you need to nail it anyway. If this describes you, check local forecasts for information about winds or use an inexpensive wind sensor, and you could describe waves in comparative terms (even video!). For large bodies of water like the Great Lakes or coastal regions there may be more specific data online, such as the Great Lakes Environmental Research Laboratory’s forecasting system.
Depth, flow, wind, and waves are must-haves, but also consider whether a site might ice over, and how much sunlight is available. Ice can ruin some buoy hull materials, which are most often a type of plastic in the case of water monitoring buoys. Too much sunlight is not typically a problem, thanks to UV-resistant hull materials that are pretty standard now. But too little sun can definitely be a problem. If you place your buoy in a shaded area, or where prolonged darkness is the norm during certain months, that can be a challenge. We’ll talk more about that when we talk about power, but first let’s talk about payload.
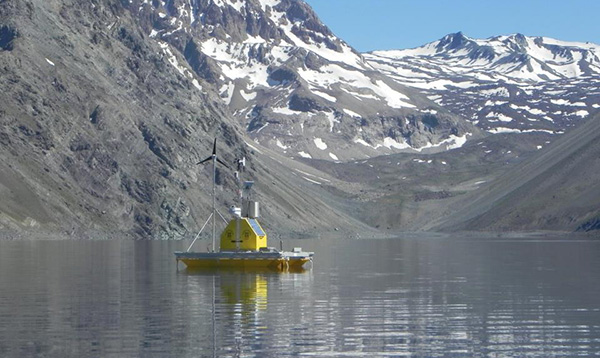
2: Payload
Payload means a couple of different things. First, there is the sensor/instrument payload—all the goodies you want to wire up to do your science, along with the dataloggers and telemetry (#3 below). But the other meaning of payload is more traditional—it’s about the weight of all those goodies and everything else that’s part of the system, like stainless steel frames to bolt all this stuff to, mooring chains, etc.
So first, consider what you want to measure, and then select the best instruments to measure it. Some of the most popular instruments integrated with YSI’s buoys include YSI’s EXO2 multiparameter water quality sondes, Sontek’s Argonaut-XR Doppler current profiler, and Aanderaa’s MOTUS directional wave sensor, which is also available here in the U.S. as part of the MOTUS buoy. And yes—it is possible to get all of these sensors in one system!

When you select the instruments, bear in mind that the point of a buoy is to do unattended monitoring. Thus the instruments must operate reliably with changing conditions that might occur and at the depth where you want measurements taken, without an operator needing to tend to them. A big issue in unattended monitoring is biofouling, which can vary a lot from site to site, freshwater to marine. Assure yourself that the technology can handle or mitigate the effects of fouling.
While YSI can integrate almost any sensor into a buoy system, even non-Xylem technologies such as wind sensors, the sensor payload will ultimately define the power and logging requirements. We certainly can add extra loggers and power subsystems that your sensors require, but where there are more sensors, there is more onboard power, and where there is more power, there is more weight.
There is an optimal freeboard for a buoy—the distance between the waterline and the top of the buoy’s hull. That distance is affected by how much weight is loaded onto the buoy. Usually the power system is the biggest load (in terms of weight), as will be discussed a bit more in #4 below. Adding batteries might drive up the size of the buoy that is needed, which of course will drive up the costs, too. If the environment has already demanded a big buoy (see #1!), sensor payload will not be the biggest driver of buoy size, typically.
In any case, expert integrators at YSI will help you figure all of this out. What you need to know is what you want to measure!
3: Logging & Telemetry
The choice of a datalogger is firstly driven by the sensor payload. More sensors means more things to plugin, so the datalogger needs to have enough ports and the right kind of ports to handle the outputs of the sensors (SDI-12? 4-20 mA? RS232 serial?). There’s always a datalogger with enough ports to handle what you need, and it is possible to have multiple dataloggers within a single system. There is also a range in ease-of-use with dataloggers. Some datalogger/sensor combinations are almost plug-n-play; others will require manual coding to coordinate timing of data collection, packaging of data for transport protocols, etc.
Sometimes it’s easier to choose the datalogger by first deciding where you want the data to go. Like the sensors, the telemetry technology is also configured with the datalogger. An external modem might even consume one of those ports that a sensor might otherwise occupy.
The main telemetry options people decide on are whether to use cellular networks, satellites, or whether a system will be communicating with a SCADA system such as at a water plant. Each option brings with it different considerations. How good is the cellular network at the monitoring site? Getting communication is one thing, but is your organization prepared to manage a cellular account? If a satellite is the preferred option, are there certifications required for the technology to communicate with the satellite of interest? Any fees?
There is also a software side to the telemetry question. It’s one thing to move the data, but what’s on the receiving end? Are data files just being stored on a network, to be opened with desktop software, or will the data be visualized in a platform like Xylem’s HydroSpere? How you want to see your data is a major consideration when building your buoy system. You can learn more about that in a webinar we did about remote data collection. [Watch Webinar: Remote Data Collection - How Environmental Scientists Work from Home]

HydroSphere Data Visualization Software Screen Shot
Of course, telemetry itself is an option. There are still a lot of people who visit their dataloggers periodically and manually download the data. This can be done with a USB drive, or via wireless or BlueTooth™, depending upon the datalogger.
We all use these types of technologies in our daily lives but rarely think about how they really work, so don’t be intimidated if this is unfamiliar territory or you’re not sure what to choose. The complexity that can arise in a buoy system, especially as it relates to logging and telemetry, is one of the main reasons YS’sI Systems Integration team is sought out all over the world. Typically we integrate the system in our factory, including setting up all the logging, telemetry, and data transport. We often send test data to the final destination before disassembling the system for shipment. It’s a lot easier to do this in the factory than on the water!
In sum, it’s great if you already know a lot of this stuff when you call us, but at the very least, you need to know where you want your data to end up. We’ll help you map out how to get it there!
4: Power
Of course, all of this stuff requires power, and it’s often the sensor payload we think about first when start considering power requirements. For example, remember in #2 above when it was mentioned that biofouling is a major consideration when choosing sensors? Deployable antifouling technologies are often very power-hungry. Shamelessly this is where I often talk about the benefits of the EXO platform’s industry-leading central wiper, which requires far less power than UV light, pumps that deliver antifouling chemicals, or air blasts used to clean some optical sensors and which require an actual air compressor.
In fact, one of EXO’s biggest advantages is that the sonde itself doesn’t require a lot of power. Lamp-based optical sensing technologies, by contrast, might require “mains” power to be operable for 90 days in the field like EXO can on C or D batteries. This is one of the reasons we are so excited about the new EXO NitraLED technology—finally there is a deployable nitrate sensor that isn’t lamp-based!
Due to their remote locations, buoy systems typically have a solar-powered battery subsystem to support all of the sensors, loggers, and telemetry hardware, as well as lanterns, beacon or other power-requiring hardware that is standard on the system. Often people have a “set it and forget it” mindset when it comes to solar power, but it’s not quite so simple.
We had a scenario once where a customer sought technical support for a buoy system that had been working very nicely, but it quit transmitting data a couple of years later. After hours of investigation of all the logging and telemetry hardware and the sensors, we came to realize that the buoy had been moved to a shady spot where it didn’t get sufficient solar power! Neither the customer nor we had asked this question first (sort of like your IT—“Is it plugged in?”). Larger panels and larger or additional batteries would have been required to support the system in its new location.
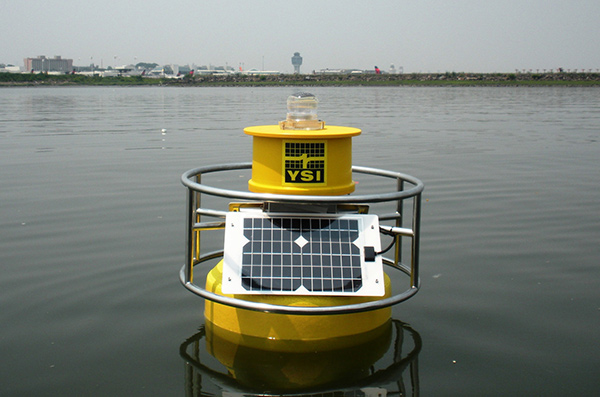
This begs the question: why wouldn’t we just always use the biggest panels and have an extra battery? The answer is twofold: cost and payload. Nobody wants to pay for more than they need, but also, a bigger power system can add a significant amount of weight. This might translate to less flexibility for adding sensors, or even the need to upgrade to a larger buoy. This has been the case when we’ve had to deploy buoys at the top or bottom of the planet—when sunlight is sparse, powering a buoy becomes a tricky business.
So what do you need to know about power when it comes to selecting a buoy? The good news is, not much. You need to carefully evaluate the intended monitoring site and be able to describe the availability of sunlight on a year-round basis, and how often sunlight is obstructed by cloud cover or weather events. We’ll help you figure out the rest—except for one thing.
You also need to think about how often you can visit the buoy, just in case you have to bring it in to make any modifications to a power system, or possibly even replace a battery. This brings us to our final topic: deployability.
5: Deployability
We can design and integrate almost any water monitoring buoy system you can dream up. But there is one detail that sometimes we all take for granted—someone has to get it in the water. 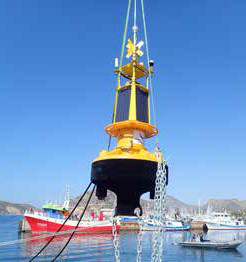
Some of these systems, like the MOTUS buoy, are so big that they’re deployed using a crane on a dock or boat. Some, like the Pisces, can be carried to a boat ramp or embankment by 2-3 people, and towed by a boat to its final location.
The new DB600 was designed by our team in Australia with deployability as a top priority. This lightweight system comes in two pieces that you can bolt together and load onto a small boat—with only one person!
Thus, thinking through the logistics of placing the monitoring buoy is something to be prepared to discuss. Don’t let limited equipment or personnel prevent you from getting the system you need, though. YSI provides services to help you with this, including services to help you maintain your system once it is placed.
That brings us to a final point to capture under the topic of deployability—serviceability. One must also think through the logistics of how sensors and equipment will be serviced on site. So it’s not just about deploying the buoy, but also about deploying people and sometimes things like calibration buffers, laptops or tablets, with some regular interval. Talk to your YSI rep if this is a challenge for you—we can help!
In closing, when it comes to choosing a buoy, start by thinking about the environment, payload, logging & telemetry, power, and deployability. Use our online tool to help you get started, and we look forward to helping you!

Additional Blog Posts of Interest
Networks that Work | The Narragansett Bay Fixed-Site Monitoring Network
Water Quality Monitoring with Vehicles for Better Coverage
For the Love of Charles | A River on the Rebound