Wastewater Treatment Solids Retention Time Control Implementation
Introduction
(Updated August 2021)
Solids Retention Time (SRT) is a critical activated sludge design and operating parameter. The selection of an SRT has many consequences related to process performance, sludge production, and oxygen requirements. the traditional method for controlling SRT is to manually adjust the sludge wasting rate based on the food-to-microorganism (F/M) ratio or mixed liquor suspended solids (MLSS) concentration. The effectiveness of closed-loop control of SRT has been demonstrated in many locations.
In addition to reducing variability in actual SRT, other benefits cited include reduced foaming, improved sludge settling characteristics, improved performance of downstream sludge thickening, and fewer laboratory process control measurements. Automated SRT control is likely to be of great benefit for overloaded or nutrient removal facilities. However, a big reason that automated SRT control is not more widely practiced is that many operators and engineers fear that a malfunction or misapplication of the control system will lead to a process upset. A better understanding of the proper application of SRT control is needed.
A review of published information and the authors’ experiences reveal how SRT control can be optimized for the most stable results. Control system design requires accounting for process dynamics, selection and location of instrumentation, and development of a control strategy. The basic components of an SRT control system include flow and level meters, online suspended solids sensors, and a PLC or microprocessor. The control handle is the waste activated sludge flow rate. The control structure and calculations differ among the various methods. Maintenance of the online instrumentation, including evaluation of data quality, has shown to be one of the biggest challenges.
The Concept of SRT
The activated sludge process is a biological process (Learn more, How to Control Activated Sludge with Online Process Control) that relies on the development of a mixed culture of microorganisms to metabolize pollutants in wastewater. It was originally developed to remove organic pollution from municipal wastewater but has been proven for nutrient removal. Design innovations have produced configurations that can remove nitrogen and phosphorus. Dissolved oxygen (DO), sludge recirculation, and sludge wasting are the three controllable operating parameters once the aeration tanks and settling tanks are in the ground. Automation of DO control is presently the subject of intense interest because of the energy required for injecting it into the process. However, SRT, controlled through sludge wasting, is the single most important design and operating parameter affecting the performance of activated sludge systems (Metcalf & Eddy, 2004).
The SRT represents the time spent by microorganisms in the system, or the time available for microorganisms to reproduce. It is also referred to as mean cell retention time (MCRT) or sludge age. Each microorganism has a characteristic regeneration time which depends on many factors. If SRT is longer than regeneration time of a particular organism, it will proliferate. Otherwise, it will be washed out of the system. For instance, the minimum SRT required for nitrifying microorganisms is shown in Figure 1.
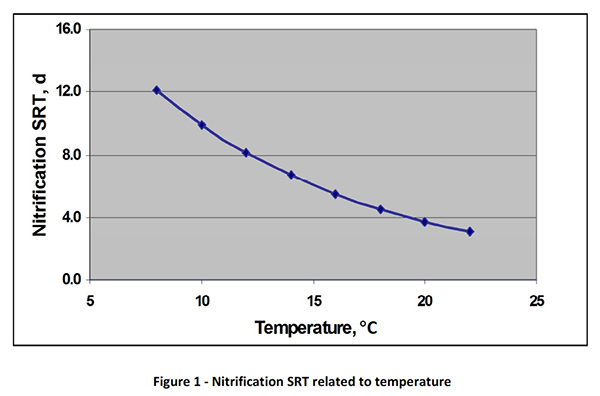
Figure 1: Nitrification Solids Retention Time Releated to Temperature
At a temperature of 20°C (68°F), an SRT greater than or equal to four days, is required for nitrifiers to regenerate at a faster rate than they are wasted from the system. At an SRT less than four days, nitrifiers will be removed at a faster rate than they regenerate, and they will be washed out of the system resulting in no nitrification occurring. A WWTP having a discharge limit for ammonia will need to maintain a sufficient SRT for nitrification to occur. If nitrification is not required, it is desirable to maintain an SRT to wash nitrifiers out of the system and minimize energy consumption for aeration because nitrifiers exert a substantial oxygen demand.
The concept of SRT, to most wastewater operators, is based on the parameter food to microorganism ratio (F/M ratio) which is the ratio of the organic load to the mass of microorganisms in the system calculated as follows:
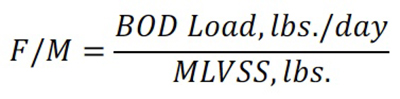
BOD load represents the influent organic load. MLVSS is mixed liquor volatile suspended solids which is a measure of the amount of biomass in the system. SRT and F/M are related by the following equation:
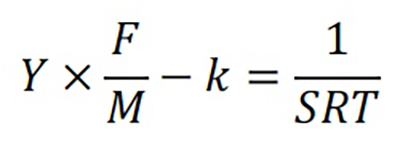
Therefore, a constant F/M implies a constant SRT because the yield (Y) and k (decay) are generally constant for a particular system. Also, the values are inversely related such that a lower F/M requires a higher SRT and vice versa.
Automation of SRT control reduces operation and maintenance requirements and improves treatment performance. Measurement of MLSS is critical to either F/M or SRT operating control strategy. The information provided by online Total Suspended Solids sensors (such as the YSI ViSolid®) eliminates the need for daily grab samples and manual measurement of TSS reducing laboratory testing requirements, often by over 75%.
Furthermore, continuous measurement and automatic calculation of SRT reduces the operator attention required. The manual strategy for SRT control is to find one or maybe two seasonal strategies that work under all conditions because the effects of a change to sludge wasting are not immediately apparent and the consequences for an improper adjustment could be dire and long-term. The alternative is to live with the inefficiencies from carrying excessive solids inventory.
Maintaining an optimum SRT through automatic SRT control also improves treatment performance. Automatic SRT equalizes sludge flow and eliminates intermittent peak loading of solids treatment processes that occurs with manual SRT control. The loadings cascade through the plant as recycle liquid is decanted and recycled back to liquid treatment. Automatic SRT control also impacts microbial community structure. In general, the higher the SRT, the more biodiversity, the more functions supported. The risk of too low an SRT is that a particular function is not supported. This is most critical for nitrification because it is the only practical approach for ammonia removal.
Furthermore, without nitrification there cannot be denitrification. On the other hand, an SRT that is too high increases operating cost and reduces treatment capacity. For example, automatic SRT control has been demonstrated to eliminate nocardia foaming by maintaining F/M within a desirable range. Another example is sludge settling. Optimum settling depends on the diversity and prevalence of microorganisms. If SRT is too low, “straggler” organisms predominate. On the other hand, if SRT it too high, pin floc occurs. A summary of the impact of SRT on activated sludge functions is shown in Table 1.
Activated Sludge Function |
Impact of SRT |
Optimum SRT |
COD Removal |
Too low: Elevated BOD in treated effluent.
Too high: Increased oxygen requirements; increased energy usage
|
As low as possible to permit development of a flocculent sludge and nitrification, if required |
Nitrification |
Too low: Incomplete nitrification; elevated ammonia in treated effluent; denitrification not possible
Too high: Increased oxygen requirements; increased energy consumption; increased nitrate (degrades denitrification performance)
|
4 to 8 days |
Denitrification |
Too low: Incomplete denitrification; elevated nitrogen in treated effluent; higher chemical usage in denitrification filters
Too high: Increased oxygen requirements; increased energy usage
|
10 to 15 days |
Activated Sludge Function |
Impact of SRT |
Optimum SRT |
Phosphorus Removal |
Too low: Enhanced biological phosphorus removal (EBPR) will not occur. Increased chemical usage
Too high: Phosphorus uptake rate is reduced. Supplemental chemical addition could be required
|
5 to 12 days |
Final Settling |
Too low: Poor settling; increased total suspended solids in effluent
Too high: Increased solids loading; filamentous bulking; increased total suspended solids in treated effluent
|
Variable - depends on treatment goals |
Sludge Treatment |
Too low: Higher sludge production
Too high: Reduced sludge dewaterability; lower sludge digestibility; reduced biogas production
|
Variable - depends on treatment goals |
Technical Enablers
The adoption of automation for wastewater treatment plants has been a slow process for several reasons. One of the main obstacles has been the inability to measure important operating parameters at a sufficient frequency to use in feedback control. Dissolved oxygen and pH were the first parameters that could be measured online. Operation and maintenance of the early versions of these online sensors was cumbersome, leading to neglect, and resulting in low data quality and eventually abandonment of the instruments. The lack of suitable instrumentation was not the only barrier.
The computing power to execute the automation was expensive and required extensive training to use. The inadequacy of measurements and computing power also contributed to gaps in understanding of the process because it was difficult to test theories full-scale. As a result there was also little incentive to develop better actuators that could modulate equipment or test the control theory needed for the wastewater application.
Measurement of MLSS is essential for the control of SRT. However, the traditional gravimetric technique for measuring MLSS has several deficiencies that limit applicability for automatic control. The gravimetric procedure is a multi-step manual technique that consists of taking a sample, filtering the sample through a previously weighed filter assembly, drying the filtered sample for at least 1 hour, weighing the filter assembly and sample, and subtracting the filter assembly. There are potential biases at nearly every step. Inaccuracies notwithstanding, a completely accurate sample may not be representative of the daily average because MLSS will vary throughout the day as loading varies. The procedure is time consuming which limits the number of measurements and adjustments. Furthermore, there is typically a delay of 2 hours or more between the sample and the adjustment. Therefore, tight control of SRT which would be required for short SRT systems, for example, is not possible. However, besides being cumbersome and subject to several potential biases, the delay between sample and measurement makes gravimetric techniques unsuitable for automatic control.
Alternatively, TSS can be determined online using scattered light or light absorbance. Under normal conditions, there is a good correlation to gravimetric analysis. Suspended solids reduce the intensity of optical radiation energy. Scattered light is the measurement of the intensity of light scattered at a certain angle including backscatter, the direct reflection of light back to the source. Turbidity is defined as the measurement of light at a 90° angle. The ratio of penetrating to emitting light beams is measured as turbidity or suspended solids. However, there is no standard for TSS measurement. Measuring angles, light sources, and a number of detectors vary among manufacturers. The highest signal intensity is observed for an angle of 90°. However, as the concentration of suspended solids increases, interference between particles also increases. Because of this, not every particle is reached by the light source and the reflected light is not detected by the receiving device. On the other hand, the relationship between backscatter and TSS is linear over a wide range but the signal intensity is much lower. A measuring angle less than 90° is a good compromise and is suitable for concentrations observed in activated sludge.
There are several potential interferences for the TSS measurement. Naturally, anything that accumulates on the face of the sensor will cause an overestimate of the concentration. Therefore, all TSS sensors include various forms of cleaning. One cleaning system consists of a mechanical wiper that intermittently wipes the face of the sensor clean. Air and water based systems use an intermittent pulse of compressed air or water to displace accumulated material. The sensor from YSI uses a vibrating ultrasound cleaning system called UltraClean technology. The promoted advantages of this method are that it operates continuously, deterring colonization from pioneering species and that there are no parts to maintain.
Approaches to SRT Control
The objective of SRT control is to manage the mass balance shown in Figure 2 through adjustment of the waste activated sludge (WAS) flow rate (Qw). The calculation is straightforward: the inventory of biomass is divided into the rate of sludge wasting. The volume (V) of the aeration tank is known, the MLSS and return activated sludge (RAS) (Xr) concentrations are measured and the effluent concentration of TSS is typically sufficiently low enough to be ignored.
Traditional Approach
The traditional method for SRT control is to maintain a constant MLSS. Manual or online samples of MLSS are analyzed and a calculation is performed to determine the volume of sludge to be wasted and the wasting pump or valve is operated or adjusted accordingly. The problem with this strategy is that it does not account for variation in the BOD load. Furthermore, MLSS is influenced by the inorganic proportion of influent TSS and the ratio of return sludge. As a result, this strategy does not achieve a constant F/M as desired.
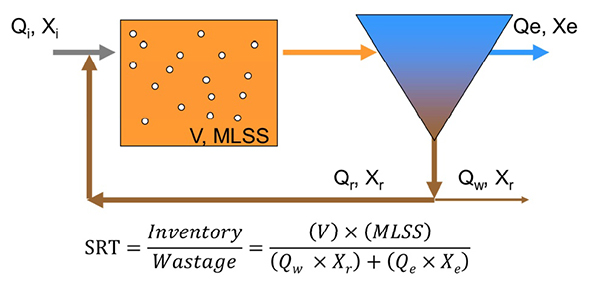
Figure 2: Mass Balance Diagram for Activated Sludge
Automated MLSS Control
A novel method for MLSS control of SRT has been utilized at an advanced wastewater plant in northern Ohio for over 10 years. The method incorporates timers, signals from online TSS sensors, manual input of the sludge settleability, and the MLSS setpoint into a controller that automatically calculates the sludge to be wasted and adjusts the operation of the waste sludge pump. A diagram of the control system is shown in Figure 3.
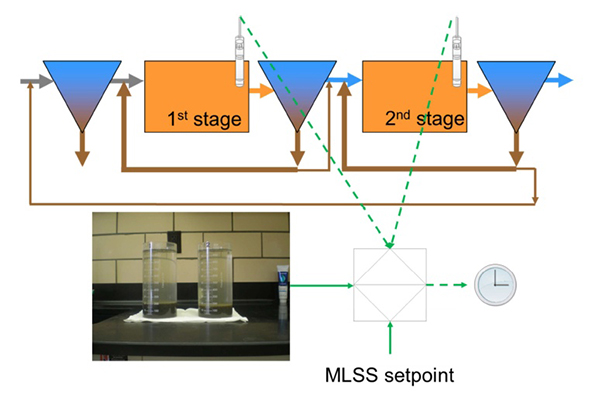
Figure 3: Automated MLSS Control
Several features are built-in to stabilize sludge wasting and guard against too much or too little sludge being wasted. First, sludge wasting is cascaded through the multi-stage system - first stage to second stage; second stage to primary – so that if an error is detected, sludge can be recovered. Second, sludge is wasted every 8 hours on a timer. This is important to steady the operation of the biological system and reduce the potential for upset, especially over weekends and holidays when the plant is not fully staffed. The amount of sludge wasted is based on the difference between the MLSS setpoint and the current reading from an online TSS sensor located at the tail end of each stage.
The amount of sludge wasted is adjusted based on the most recent. hour settling test result entered by the Operator to prevent too much or too little wasting if sludge settleability changes or the sensor calibration drifts unexpectedly. Routine maintenance of the ViSolid® sensor is performed to ensure the highest accuracy. A single-point calibration is performed weekly by simply adjusting the sensor reading based on a laboratory suspended solids measurement from a sample taken near the sensor. The cleaning system prevents fouling of the sensor. However, for good measure, the sensor is cleaned every three weeks by simply wiping it off with a damp rag. In total, maintenance requires not more than 15 minutes of operator attention per week.
Hydraulic Control
Hydraulic control is the simplest method for SRT control because it requires only a waste sludge flow measurement. MLSS is wasted directly from the aeration basin in the Garrett method. The waste sludge flow rate is calculated simply as the known volume of the aeration basin divided by the desired SRT. For example, if a ten day SRT is desired, then 1/10th of the aeration basin volume is wasted per day. The main drawback of this configuration is that the volume of waste MLSS could be two times or more the volume of WAS such that sludge thickening facilities need to be built significantly larger. Because of this, the Garrett method is utilized at very few facilities. However, the Garrett method has been utilized at Kalamazoo, MI, Houston, TX and Madison, WI for many years.
A novel method for hydraulic control from the RAS line was developed as part of a trial study at Collingwood, Ontario. The method, shown in Figure 4, is based on a mass balance around the final settling tank that rearranges the SRT formula in terms of wastewater and RAS flow as follows:
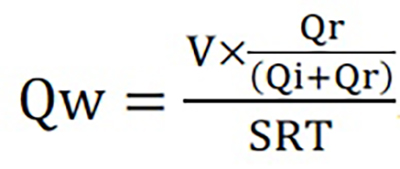
The method does not require solids measurements but there is also no feedback which is uncomfortable for many practitioners.
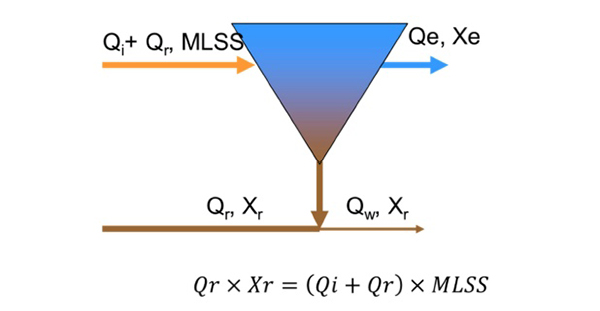
Figure 4: Hydraulic Control of SRT Based on Flow Measurements
Solids Control
This concept involves automation of SRT control using online TSS measurements. It is the basis for multiple commercial SRT controllers including the SIMS controller by Sanitaire, the Royce Model 7700 SRT Control System, and SRTMaster™ by Ekster and Associates. A controller can be designed to control sludge wasting based on a setpoint SRT with input from online TSS sensors. However, the controller algorithm must take into consideration the non-steady state nature of SRT and validation of online sensor readings. A smoothing algorithm is required for the SRT equation to be used directly in activated sludge.
For example, SRT does not double instantly when the waste rate is cut in half. This is accomplished by calculating a moving average or by using a dynamic calculation, for example, dynamic sludge age (Vaccari et al 1988). The San Jose/Santa Clara Water Pollution Control Plant San Jose uses a portable solids probe to calibrate each process instrument. The portable instrument is calibrated 1 to 4 times per month with laboratory data and used to adjust the calibration of the online TSS sensors. Periodic suspect sensor data was evaluated using a statistical method. Safeguards were implemented to interrupt the solids wasting algorithm in the event that “bad” measurements were detected.
The Southwest Water Cornborough WWTP is believed to be the first system to implement automatic SRT control in Europe. The main challenge was to maintain compliance despite wide seasonal variations in loading. An SRT of 3 to 4 days was desired to maintain good sludge settleability and to prevent the onset of nitrification which wasn’t required by the discharge permit. Furthermore, an automatic system was needed to accommodate limitations in the solids handling capacity of the plant (the location included a regional solids handling facility). The plant was one of several in the district staffed by operators of various experience levels on a rotating basis complicating manual control.
A comparison of sludge settling for the Cornborough facility implementing automatic SRT control and a similar facility in the district not implementing automatic SRT control is shown in Figure 5. The stirred sludge volume index (SSVI) is lower and more stable at Cornborough. The improvement in the manual control towards the end of the period is a result of the operators at the other facility trying to manually match the control strategy observed at Cornborough demonstrating the benefit of automatic control even without instruments or controller hardware installed!
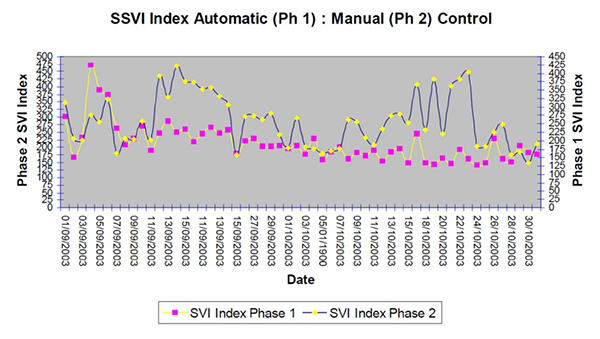
Figure 5: Comparison of Sludge Settling Under Manual and Automatic SRT Control
A demonstration project in Tillsonburg, ON demonstrated a novel method for SRT control that reduced the requirement for online TSS sensors. The MLSS concentration was calculated in real-time using a mass balance around the aeration basin as follows:

The calculated MLSS was inserted into the SRT equation eliminating the need for a MLSS measurement. Another reported benefit of this method was that it eliminated the need to calibrate the RAS TSS sensor as long as there was a linear correlation with solids concentration. An inaccurate RAS measurement would be compensated by an inaccurate MLSS calculation and the two errors would cancel out in the SRT equation. The drawback of this method is that it lacks feedback and it requires estimate or measurement of the influent solids concentration (Xi) and growth rate (R), although these terms would be small compared with the remaining terms and could be neglected.
An effective SRT controller has several features, regardless of the approach. Most importantly, it is slow. The rule of thumb is that it requires three solids retention times until the effects of a change in operation are completely observed. It is transparent. The authors have observed that operators are reluctant to activate automatic SRT control when they do not understand how it works. It has fault detection. This is perhaps the most technical component of automatic SRT control because the controller has to be programmed how to detect faulty sensors or malfunctioning equipment and default to a safe operating point. It has multiple operating modes. The controller should be able to act as a stand-alone device, to output calculation to a central SCADA system, or to make the calculation only and leave the manual adjustment up to the operator. For most facilities, the latter mode should be the starting point until operators understand controller operation and learn to trust the recommended adjustments. Last, and very important, the controller has to include sufficient training and an extended period for support. The ability of the controller vendor to observe or even take control remotely is highly desirable for the first several months of operation.
One of the biggest benefits of automatic SRT control is improved treatment performance. The WWTP likely to achieve the greatest benefit in this regard will have one or more of the following characteristics. Facilities operating close to design points will benefit from keeping a manageable and not excessive solids inventory. Likewise, facilities that experience a wide range of loadings will benefit by gradual automatic adjustment of the SRT to keep it near an optimum level and lessen the likelihood of annual upset events during transition. Stringent effluent nutrient limits, particularly for phosphorus, require an optimum SRT. Too low of an SRT and nutrient removal functions are not supported. Too high of an SRT and treatment degrades. Keeping SRT below the nitrification threshold at facilities not required to meet a low ammonia limit will reduce operating costs for energy. Automatic SRT control can also be a tool to train and lessen the burden on inexperienced or part-time operating staff by encoding the knowledge of experienced engineers and operators into the algorithm.
Summary
Heretofore, automation of SRT control has not attracted much attention even though SRT has a significant impact on every function of a WWTP. Part of the reason is related to the lack of suitable instrumentation and control algorithms. This is no longer true. Several suitable instruments and control strategies now exist and have been demonstrated to be effective. The case studies presented here demonstrate some of the benefits of automatic SRT control. Currently, a bigger challenge is increasing the comfort of operators who have been accustomed to infrequent manual control based on laboratory measurements and well-earned intuition about the needs of the process. Nonetheless, the trend is towards greater automation due to more stringent treatment requirements, shrinking capital and operating budgets, and turnover of operations staff due to retirements.
Authorship
Dr. Robert Smith, PhD, PE, BCEE - Applications Engineer, Wastewater at YSI, a Xylem brand
Sarah Elger, PE, MSEV - Process Engineer, Biological Solutions Group at Sanitaire, a Xylem brand
Scott Mleziva, BSEE - Electrical Systems Supervisor, Biological Solutions Group at Sanitaire, a Xylem brand
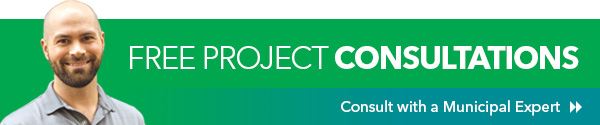
Additional Blog Posts of Interest
How to Control Activated Sludge with Online Sensors
Activated Sludge | Three Steps to Improve Your Process Efficiency
How Orthophosphate Monitoring Cut Costs by 25 Percent
Chemical Oxygen Demand in Influent Wastewater Monitoring