Total Suspended Solids Monitoring For Process Stability
Problem:
Inconsistent secondary clarifier performance limited the quality of effluent an advanced wastewater treatment facility in Kansas could produce. The Operations Engineer sought to achieve the lowest Total Suspended Solids (TSS) and most consistent effluent by controlling the solids retention time (SRT). (Learn more, Implementation of Solids Retention Time Control in Wastewater Treatment).
In order to implement this solution, a new monitoring system was required for continuous online measurement of TSS in the mixed liquor suspended solids (MLSS) and return activated sludge (RAS). The desired characteristics of the new monitoring system were long-term accuracy and simple maintenance. Furthermore, it had to be applicable at the other facilities owned by the utility.
Solution:
Based on project specifications, three monitoring system suppliers were selected for an on-site demonstration. The competing TSS sensors were placed side-by-side in an aeration basin and performance was compared over a 2-month trial period. Accuracy was verified with gravimetric analysis of grab samples collected near the sensors and maintenance activities were logged.
The system from YSI, a Xylem brand, had the highest accuracy, the least maintenance, and was selected for permanent installation. IQ SensorNet ViSolid TSS sensors were installed at the oxic end of each of the 4 treatment trains to monitor MLSS. Additionally, insertion mounted ViSolid sensors were installed into RAS pipelines. According to the Operations Engineer, “If it works in MLSS it will work in RAS”, because RAS is just concentrated mixed liquor. Measurements from the sensors are output to the SCADA system through 4-20 mA signals. The target SRT is maintained by automatic adjustment of the sludge wasting rate using a formula programmed into the Allen Bradley PLC and calculated using the online monitoring data.
Pictured below: ViSolid® 700 IQ inserted into a RAS pipeline through the retractable armature.
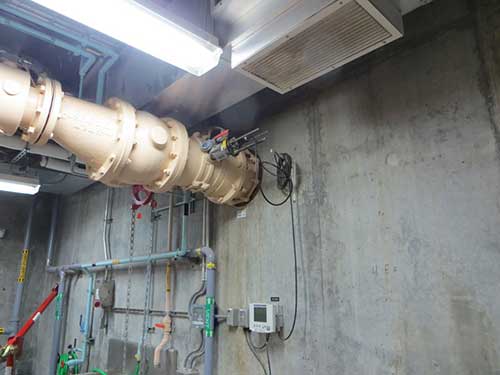
Results:
The monitoring system at the facility has been operating reliably for years with minimal maintenance requirements. The UltraClean ultrasonic cleaning system effectively prevents fouling, without a wiper or any replaceable parts. Sensors are removed from the process and manually cleaned every 6 months.
The IQ SensorNet system has also been successfully implemented at 2 other facilities owned by the utility. The Operations Engineer has been a steady, guiding force but admits that success cannot be achieved without staff involvement when he states, “Proper implementation (of process monitoring and automation) requires a long term relationship – champion it, believe in it, get it right, then get the operators on board.” This attitude has produced award-winning performances. Two of the facilities owned by the utility have earned Platinum status from the National Association of Clean Water Agencies (NACWA) for excellence in permit compliance.