Aquaculture Facilities Benefit from Continuous Monitoring & Control
Video Transcription
Transcript by Speechpad
Darrin: Thank you, Theresa. So today, we're going to do an overview of the M&C (monitoring and control) instrumentation. So basically, what we’ll go over is Aquaculture, Aquaponics, Live Haul, Aquarium, and Research where you can use those instruments for any of those applications. We'll also go over the expansion modules. So they're fairly new, and we'll have the ability to have 4 to 20 milliamp inputs, 4 to 20 milliamp outputs, and additional relays. We'll go over some monitoring and control applications, and the Feed Smart timer, and some sensor placements, and how to install them properly.
To start off, the 5200A is multiparameter, measures dissolved oxygen, pH, conductivity, salinity, ORP, and temperature. The 5400 is a multi DO. So we have up to four DO and temperature sensors. And that uses a galvanic DO sensor. And last but not least, with the 5500D, it's an optical DO, and it can use up to four DO sensors. There are actually three different models. We have a single channel, a dual-channel, and a four-channel. So with the optical, it gives you a lot easier to use the sensor, a lot less maintenance. It's more accurate. Now, keep in mind all three of these instruments you can use an AC version or DC version. And with the AC version, you have a 12-volt battery backup option.
The new IOEM expansion module gives you the capability of adding to the system. So you can add inputs such as 4 to 20, 0 to 1 volt, 0 to 5 volt, or digital input. So we can use third-party sensors such as pH, and ORP, flow, total gas pressure. A nice thing with that is we actually provide the 24-volt isolated power for those sensors. We also have the ability to do a 4 to 20 milliamp output. So we can control pumps, valves, VFDs (variable frequency drives), you know, control, or go back to a PLC or a SCADA system. On the IOEM, you can actually have a 120-volt or a 12-volt power.
The REM, which is a relay expansion module, gives four additional relays to add to any system. The 5200A, 5400, and 5500D already have relays, but you can actually put these anywhere you want within the network. And that way, you can reduce the amount of wiring and everything. You're only running one wire to these expansion modules. The four relays are just a dry contact relay. So it can be powered with the AC or DC power. And it can be powered by AC or DC.
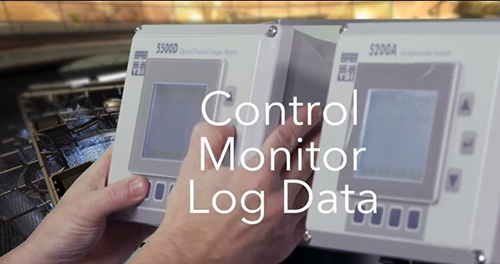
So now, we're going to have Tyler talk about some monitoring and control applications. So here's Tyler.
Tyler: Thanks, Darrin. Our Aquaculture instruments offer flexibility in the ways you use them. In addition to the native center support for the standard parameters on 5200A and 5500D systems, you can also connect a variety of peripheral sensors and instruments using the analog inputs for either device.
These instruments can be used to control your life support systems. Customers all over the world are using our instruments to control aeration pumps, filtration systems, UV disinfection systems, lighting, automated feeders, and many other devices that make running a production facility more efficient. With the addition of our new IOEM modules, you can now output all of the feedback from our controllers to a centralized PLC or to any other control systems that accept an analog input. Our instruments also ship standard with up to eight dry-contact relays. These can be used to control alarms, heating elements, up, and AC and DC power devices.
Many aquaculture facilities prefer the flexibility of the analog outputs. Existing PLC and SCADA systems can typically be equipped with analog input cards that allow you to connect your YSI devices for integrated data logging and remote monitoring.
If you don't have a PLC or SCADA system, AquaManager can serve a similar function with no professional integration services required. In this example, we'll be controlling DO in a raceway using a 5500D, an IOEM, and a series of pumps and variable frequency drives or VFDs.
To begin, your 5500D will continuously monitor analog conditions for DO and temperature. At the same time, the instrument is sending the sensor data to the IOEM modules. This module is configured to scale the analog output to the measured parameter. You can scale these parameters however you'd like, but we recommend using the full zero to 20 milligrams per liter scale for dissolved oxygen. The analog signal is received by the VFD. The VFDs are programmed so that if the DO value falls below 5 milligrams per liter, the pumps will ramp up from their regular nominal frequency to a scale of the frequency that corresponds to the analog input value. If the DO falls below three milligrams per liter, the VFDs are programmed to run the pumps at full frequency for these pumps. That's 60 hertz.
If the system loses communication due to a power failure or other malfunction, the VFDs will automatically interpret that zero milliamp signal from our instruments as an alarm and run the pumps at a designated safe value. The pumps will then run continuously at the program's speed until the values from our instruments begin to change. As the raceway gets closer to its optimal DO value, the pumps will return to their nominal state to save energy and reduce the stress imposed on your socket. Many modern VFDs offer a feature to output an energy consumption value as well. This information is received by the IOEM and scaled to a kilowatt value. This can be logged and used to estimate energy costs or to monitor pumps remotely and identify pumps that may require service. This process is carried out any time the VDF is receiving a signal from the IOEM. During sensor cleaning and maintenance, the 5500D can be put into a service hold mode to ensure that the system remains stable.
In addition to analog outputs, you also have the freedom to control connective equipment directly with dry-contact relays. The 5500D is equipped with eight of them, and the 5200As have four. These relays act as an automated switch to turn devices on and off depending on a timer or a sensor value range. Many facilities use these relays to trigger a physical or a software alarm to alert personnel of conditions that might require their attention. They're also frequently connected to an autodialer, so you can have backup remote alarms in case there's an equipment failure elsewhere in your facility.
As with the analog connections, the 5500D continuously monitors the parameters for connected sensors, DO in this example. As it's programmed on the instrument or in AquaManager software, the relay will switch automatically if DO is outside of its user-specified range. This can also be accomplished with an REM if you're using many relays and don't have enough at the instrument. Once switched on, the relay will either supply or cut power to the connected device. If the device were a pump, like in this example, the normally opened relay will close and allow the flow of electricity to the pump. While the connected devices are active and attempting to stabilize near the setpoint value, the instrument will continue to monitor all parameters and respond accordingly. Once the DO value is back to its user-specified range, the relay will switch once more, killing the power to the pump and returning to a monitor-only state.
While it's possible to configure these set-points directly on the instruments, it's a lot easier to use the AquaManager software. This string here is exactly what you'd see in the system's management dialog for a 5500D with four sensors. The arrow on the screen right now indicates the slider that you would see to set your ideal DO set-point. You can move the slider with the mouse or double click it to type in a value. The slider indicated here, defined in the first point, that triggers a low DO condition, if the measured value is less than or equal to the specified low one value, the associated relay function would start. Much like the low one slider, this slider defines the first point that would trigger a high DO condition.
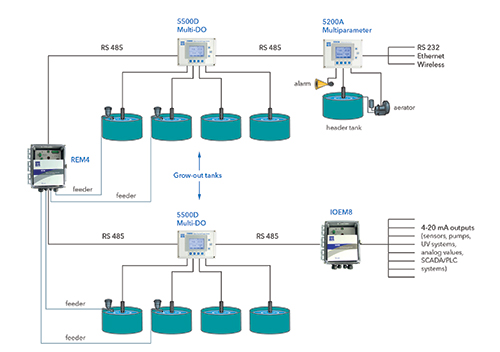
For applications that require lower DO, like hypoxia research, this would typically be associated with a value at which to trigger a solenoid to open and force nitrogen gas through an aerator to bring DO back down to your experimental values. For production Aquaculture facilities, it's pretty unlikely that you would use this function. These secondary sliders for High and Low DO conditions are used when a secondary relay is in use, that more rapidly respond to high or low oxygen concentrations. These sliders control when the alarm will be activated for each parameter. They should be set far enough away from the set-point that you don't receive nuisance alarms in the event that you use remote or physical alarming systems. Each alarm condition can be associated with its own relay. And lastly, these drop-down boxes are where you would choose which relay to associate with each condition. The relays can be named in the setup tab if you're trying to simplify the process.
The built-in relays in YSI aquaculture instruments offer a tremendous amount of design freedom. They can be used to link pH sensors and used to maintain a desired pH level. Or you can use them to activate and deactivate chemical and optical disinfection systems based on an ORP reading. You can also use them with our built-in Feed Smart software included with AquaManager to feed your stock at variable levels, depending on DO and temperature optimized feeding efficiency. Darrin is going tell us a little bit more about that.
Darrin: Thank you, Tyler. Okay, so we're going to talk about the Feed Smart feed timer. It is standard in all the monitors, so the 5200A, the 5400, and the 5500D. All have the feed timers built in. The 5200A actually has one, where the 5500D and the 5400 have four separate feed timers. They can be set up from the monitor or from the AquaManager desktop software. It can be used with most powered feeders and could have up to 255 feedings per day. We can decrease the amount of feed by using the parameter control, and that's based on the DO, temperature, and pH values. On the 5400 and the 5500D, it is just DO and Temp. We could also increase the feed amount based on the FCR or the Feed Conversion Ratio. Feed amounts can be determined by rate-based calculation. How that works is we do a calibration on a timed basis, and then we weigh the feed and put that into the instrument. I'll show you that a little bit later. Units of measure, as you can see, we have ounces, pounds, kilograms, grams. All those are user selectable. And it can be used with an REM module. So you can actually have an REM across the room so it's right next to the feeder controls, and it saves a lot of time on wiring. We have two different setups. One is continuous mode. So basically, it starts at midnight and ends at midnight for a total of 24 hours. So if you're feeding for 12 times a day, it does it every 2 hours. Or if you're feeding, you know, 48 times, it's going to feed every half hour and so on, okay? On the timed mode, it starts at a certain time, user inputted time and a user inputted time to stop. So in this case, this example, we're doing 8:00 a.m. to start, 8:00 p.m. to end, a total of 12 hours. We're doing, you know, 12 feedings, so we're feeding once an hour again.
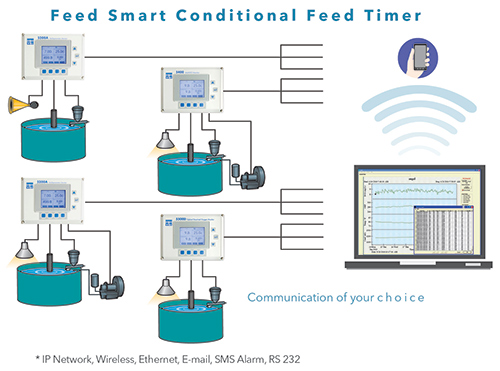
So in AquaManager, this is how you would set it up with the Feed Smart. So first, you would select which feeder you're wanting to control. Again, this is a screen shot of a 5500, so you do have the four different feeders. Next, you're going to select the relay that you want. Again, this can be an internal relay to the monitor or it can be an REM, you know, across the room or what have you. The scale, you're just going to pick and choose what scale you want. You have the "Start" and "End Date", the days you want to feed, so you can pick and choose which days you want to feed on that, the "Daily Feeding," so again, this can be up to 255 feedings per day, the "Feed Mode," so it can be either timed or continuous.
>>> Ask a Question
In this example here, it's a time mode starting at 8:00 a.m. and ending at 8:00 p.m. On the continuous mode, the "Start" and "End Date" or end time is grayed out. And then the "Daily Weight," so this is the weight that we're going to feed for the complete day. That's going to be divided by the daily feeding, which in this case is 30. "FCR," that's built in as well, and you can have that enabled or disabled. If you have it enabled, you're going to input the biomass, the feed percent mass, and the FCR factor. All those are user-inputted values. And "Sensor Control," so you have, you know, the DO and temperature on the 5500 and the 5400. In this case, if the DO drops below five, it's going to reduce the amount of feed by 9.99%. And then if it drops each tenth of a milligram per liter, it's going to reduce it again by that 9.99%. And then the "Feed Calibration," so in this case, we're turning the feeder on for 15 seconds, having someone underneath the feeder with a bucket. It's going to be turned on. Feed is going to come out. After the 15 seconds is up, we're going to weigh it and put that measure value into the instrument. Now, we recommend doing this at least three times and then doing an average just so you get the best accuracy.
So here's just an example of a calculation in "Time Mode." So we're going to do the calibration for 15 seconds. We're going to weigh the feed. It's going to be 243 grams, and then the rate is 16.2 grams per second. The start time is 8:00 a.m. The stop time is 8:00 p.m., so a total of 720 minutes. The daily weight is 1900 grams. We're going to feed 30 times per day. So that is 63.33 grams per feeding. The feeder will be actually on for 3.9 seconds, and then the times between the feeds is 24 minutes. So in this case, every 24 minutes the feeder is turned on for 3.9 seconds and put out 63.33 grams of feed.
So here, we have an example of a feeder and DO control. This customer here actually has seven tanks that were monitoring DO and Temp and then controlling feeders. They have a total of two 5500Ds and two REMs. You can see a picture there. And for the DO control, we have eight solenoids. We have a total of seven tanks. We have one control for each tank, and then we have an emergency. So what happens is, in the emergency, all the tanks are being fed with oxygen just to boost everything. And then we have seven feeders controlled by the 5500 and the REM as well. So DO control settings for that customer. You can see the set-point is at nine milligrams per liter. The low one is at six, and that's going to turn on relay number four on the O2 module, which is an REM. And if it drops below four, then it turns on the emergency. That emergency is actually connected to all seven tanks. So when the emergency goes on, it puts oxygen to all seven tanks. And then last, we have a DO alarm. So at 3.7 milligrams per liter, we're actually going to turn on a Sensaphone connecting that to an autodialer. And then, we're also sending out an email and text message as well. So here's just a screen shot of that facility. You can see at 6:00, it's turning it on, turning on the oxygen, and then at 9:00, it turns it off. Now there is some residual there, you know, for the line not being cleared out. So there is some oxygen left in that so that's why it’s going above nine.
Another application for DO and temperature control, we actually have the 5500. We have four raceways. There's four DO and Temp sensors connected to that 5500 hundred, one in each raceway. We have a blower that's supplying the oxygen. And then we have a flow switch within that line. So anytime that flow switch is not sensing any flow, we actually trigger the backup blower. There's a latching switch. So how the latching switch works is, if we supply power to it, it latches and turns on the backup blower. And then you have to physically turn it back off to get the primary blower to turn on. So applications like that are really good for backup blowers because if the flow switch turns it on and you got flow, well, it's going to turn it right back off because it noticed it had flow.
A heater, so if we're heating all four tanks, individually, of course, I don't have enough space here to draw all four, but we are controlling each raceway separately. And then we can do oxygen and ozone. There's another application that we're doing, again, another 5500. We have a tank, an LHO, and this customer has several of these setups like this. This is just one of them. And so at each LHO, we have a float switch. That float switch actually controls the oxygen and the ozone going into that LHO. So if the float switch actually goes below the set-point, it actually turns off the oxygen and ozone into that LHO so it doesn't go out into the air. We also have an ORP sensor in the LHO, and that also controls the ozone. So if the float switch is up, then the ORP is in control of the ozone. If the float switch is down, it is always turned off. The ORP has no control. We also have a DO and Temp sensor in the tank, and when it notices the DO in the tank gets low, we actually turn on aeration in the tank. And also, if the float switch is triggered and turns off the oxygen at the LHO, that automatically turns on the tank aeration. Now, here is just an example of the 5500, and the control at the tank, and the controls at the LHO. You can see there, there's an automatic switch, so you can turn on auto, on, or off. So they have the ability to keep it on if they wanted to, to override the controls.
So we'll be having a new app coming out. It's for the iOS app. So we'll have the ability to look at your data, look at the functions of each individual instrument, whether it's in control, whether it's in alarm, or everything's running normal. And then, we can actually look at current data and see if there are any alarms. We can reset that alarm from the app. And then we can look at historical data and zoom into that. We can look at it in portrait mode or landscape mode in all different screens. So you can zoom into each screen and everything as well.
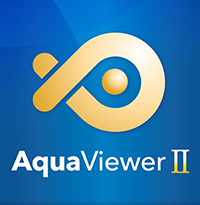
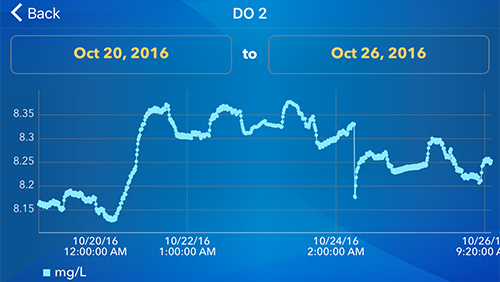
Okay, so Tyler is now going to talk about the sensor location and some of the other sensors.
Tyler: All right. So during the design phase and planning of a new facility or retrofitting an old one, making an informed decision about where to locate your sensors is essential to getting quality data. Raceways, in our experience, typically exhibit pretty uniform flow and generally stratified characteristics. So placing your sensor at any point of the raceway is usually acceptable, unless you're aware of dramatic changes in temperature within the water column. Depth typically isn't a concern as long as the sensor is placed deep enough that the sensor is always submerged. Smaller systems in round tanks can exhibit different flow characteristics. So we typically recommend mounting your sensor near the middle of the tank and deep enough so it'll never be in the air. When placing your sensor, just make sure to consider several physical factors that could affect the quality of your data as well, like the location of your aeration equipment, heating elements, feeders, and the general flow and mixing characteristics of your raceway or tank. Minimum water depth is pretty important for all sensors because if any of them are exposed to air too long, it can cause damage to the sensor that might require new sensor caps or electrodes.
We pretty frequently get asked about what to call each part of the sensor, and until recently, I don't think we've explained it very much. So generally, this is what you would see with a 5500D. This is the optical dissolved oxygen sensor assembly. And we usually refer to the larger part of the sensor as the sensor body. And there's a temperature sensor that looks like a silver button. It's not shown in this picture, but that is what that silver button is. At the end, you have the optical dissolved oxygen sensor cap.
>>> Request a Quote
5200A is a multiparameter instrument, so you have a few more sensors on this one. We refer to the housing that all of the sensors are installed to as the sensor bulkhead. The DO sensor is the shorter sensor with the membrane cap. And your pH or ORP sensor may either be a combination sensor or just pH. It usually has one or two glass bulbs on it. The conductivity/temperature sensor is the black sensor with the holes and the piece of metal protruding from the end. We also offer a few peripheral sensors that you can connect using those analog connections we talked about. This is an MJK (a Xylem brand) pH sensor. They also offer ORP electrodes for this one. And they've designed this one so it can be threaded into their own mounting option or installed directly in a pipeline. The selector ring is used during calibration and can be removed if you don't want to leave it on. And the sensor body is stainless steel. The electrodes on this particular sensor are user-replaceable, so you don't have to send it in for service when your electrodes end up failing.
Well, that's all we have, but if you guys have questions that either don't get answered today or you don't think of till later, feel free to contact Darrin or I directly. And you can see what we're up to on Facebook, Twitter, LinkedIn, or YouTube, where you can find more training videos on different instruments.
Customer Questions
Theresa: Thank you, Darrin and Tyler. We do have a few questions. First one being, "How often does an optical DO sensing cap need to be replaced?"
Tyler: So typically, the optical DO caps last around a year. I think the only time you'd see any different is either if it dries out or if it's been exposed to alcohol for any extended period of time. Alcohols will peel the paint layer right off the end of it, so we advise against using any application where it might come in contact with that.
Theresa: Thank you, Tyler. Okay, on to the next question. "How sensitive, in terms of accuracy and precision, are your pH sensors? Would an EXO YSI pH sensor be accurate enough for hatchery use? If not, do you have any advice for the best way to monitor shellfish hatchery, pH or aragonite?"
Darrin: Okay, so our pH sensors have an accuracy of plus or minus 0.2 pH units. Pretty sure that's the same for the EXO as it is for like the 5200A or even the MJK pH. Generally, that's pretty standard and what most people use. So yeah, it would be sufficient for monitoring shellfish hatchery, and for the pH, and other sensors.
Theresa: Great. Thanks, Darrin. Next question, "How often do the sensors need calibrated?"
Darrin: Okay, so yeah, this one's kind of a tricky question just because, you know, every application is a little bit different. You know, with a monitoring system, it's going to depend on biofouling. It's going to depend on what you're raising and how clean the water is and all that stuff. So what we kind of recommend, you know, when pH and ORP...I would probably look at those, you know, kind of at a weekly basis to start out and, you know, just to test it and see, "Are we in spec?" If I'm in spec, well then, don't calibrate it, and put it back in the water, and let it go another week and so on. And then, you'll get a period of time when you start to noticing drift, and again, each application is going to be different. And that goes along with the DO, the pH, you know, all of the sensors.
Theresa: Thanks, Darrin. On to the next question. "If we wanted to add additional sensors, are we able to add additional DO sensors?"
Darrin: You can add additional DO sensors using either a 5500 or a 5400. We do not have sensors that have the 4 to 20 milliamp outputs, so we can't really just add those to a existing system. You know, we did that just so you can add another 5500 and have that more capability with four or more sensors, eight more relays, four more feed timers and all that. I mean, there are other sensors out there, but again, I don't think any optical sensors have a 4 to 20 out.
Theresa: Great. Thanks, Darrin. Okay, another question. "Does the 5200A have an optical sensor or a membrane sensor?"
Tyler: So the 5200A uses an electrochemical sensor, just like you'd see on a lot of our handheld instruments. Unfortunately, there's not an option that have a multiparameter instrument that can be used for this application with an optical sensor, so yeah, just electrochemical at the moment.
Theresa: Thank you, Tyler. Okay, next question. "Can the IO system be used with a third party equipment? If so, how would I connect to it?"
Darrin: Okay, yeah, so it can be used with, you know, a third party. Basically, it's a 4 to 20 milliamp output. So that's a two-wire system. You can connect that up to a PLC or, you know, anything that accepts that 4 to 20 milliamp signal. It actually can supply the 24-volt loop or not. You know, so it can be hooked up to any system that accepts a 4 to 20. Also, if you're wanting to use additional sensors to connect up to the IOEM, we can accept 4 to 20 milliamp signals, 0 to 5-volt signal, 0 to 1 volt, and a digital. So a digital would be like a float switch, whether it's on or off.
Theresa: Okay, on to the next question. "How much manual programming is required in order to set up control functions?"
Tyler: So depending on the sophistication of your control system. It can be a lot or not a whole lot. In the example, we talked about where we were controlling ozone with an ORP sensor. It's a particularly large facility, and that was quite a bit a manual programming involved. Generally, just for DO control with relays, it's not a whole lot of programming at all. It varies pretty widely, depending on the application and the scale of your system.
Theresa: Thank you, Tyler. "I am using a ProODO handle probe. Temperature of the sensor is giving higher temperature compared with analog measurements. Can I calibrate it, or do I need to change the probe?"
Darrin: Well, that's interesting because you can't calibrate the temperature. So, you know, it depends on, you know, what is wrong. Is it either a temperature sensor on the ProODO, or is it a temperature sensor on the other device, the analog device? So yeah, unfortunately, you can't calibrate them. You know, but we can, with our monitors, we can do scaling. So if it's on your monitor compared to the handheld, then it might not be scaled properly. So you could...you might have to look at the scaling, but if it's another handheld, then we just see to determine which instrument is correct.
Theresa: Okay, I think we'll do one more question here. "Can your systems control the on/off of a 30 horsepower cooling tower fan based on inflow water temperature?"
Tyler: So yeah, depending on what kind of resolution you wanted to control that with. You could control it with relays or with a 4 to 20 milliamp signal. If you were to choose relays, you just want to make sure, for a 5500 or 5200, that you keep your amperage under 10, I believe it is, but 5 for the relay expansion model. Yeah, I can't imagine that would prove too difficult.
Theresa: It looks like a few more questions came in, but we're going to wrap up today. And we'll be sure to follow up with you afterwards if we were unable to get to your question today. Please take a few minutes and complete the survey at the end. It's only five questions, and it should only take you a few minutes. That way, we can better serve you for future webinars. We really appreciate you attending today's Aquaculture Monitoring and Control presentation. And we hope that you found it useful. And we hope to see you for the next one. Thank you.
Additional Blog Posts of Interest
Automation Leads Organic Shrimp Producer to the Forefront
Newport Aquarium's Rare Sharks Benefit from Continuous Monitoring
Automation Fine-Tunes Aquaculture Production Efficiency and Increases Profits
Pond Based Aquaculture | Dissolved Oxygen Management and Related Costs